Konventionelle Palettierung: Die Evolution Der Fertigung
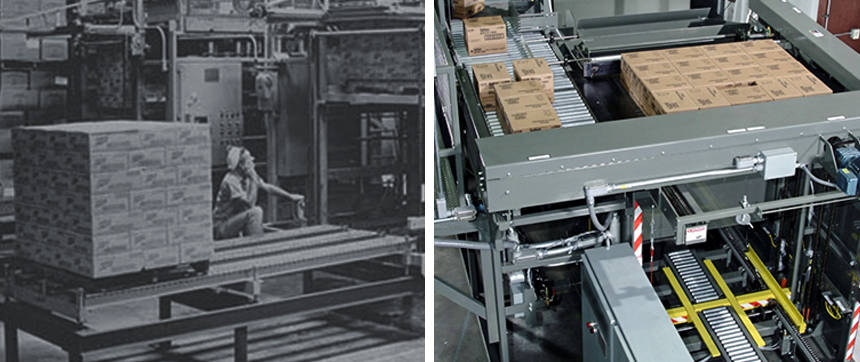
# Sie haben doch sicherlich ein Auto, genauso wie Ihr Vater eines hatte und vor ihm bereits Ihr Großvater? Was diese drei Autos miteinander gemeinsam haben, ist, dass man mit allen von A nach B gelangen konnte. Doch überlegen Sie mal, was Ihr Auto heute alles kann, das das Auto Ihres Großvaters vor 60 Jahren nicht konnte. Das gleiche gilt auch für konventionelle Palettierer. Die Technologie entwickelt sich weiter, und damit auch die Palettierung.
Um zu wissen, was Sie brauchen, müssen Sie wissen, was Sie bereits haben. Um die Technologie hinter konventionellen Palettierern besser zu verstehen, lohnt sich ein Blick auf die Entwicklungsgeschichte einer solchen Anlage.
Bereits in den Anfängen des Konstruktionsprozesses werden verschiedene Aspekte in die Überlegungen einbezogen. Das Team muss nicht nur die spezifischen Herausforderungen Ihrer Branche kennen, sondern auch Lösungen finden, um diesen zu begegnen. Neben Geschwindigkeit und Wartung sind Bedienerfreundlichkeit und Sicherheit unerlässliche Faktoren für eine Lösung, die den Anforderungen gerecht werden soll.
Konventioneller Palettierer sind bereits seit einiger Zeit auf dem Markt, gehören aber noch lange nicht zum alten Eisen. Hier erfahren Sie, weshalb sie noch immer an der Spitze stehen.
GESCHWINDIGKEIT
Konventionelle Palettierer bieten oftmals die schnellste Möglichkeit, End-of-line-Prozesse zu handhaben. Dies liegt daran, dass sie nicht auf die Bewegung eines einzelnen Roboterarms angewiesen sind und damit höhere Ausführungsgeschwindigkeiten erreichen. Durch die Ansammlung des Produkts auf dem Förderband wird eine kontinuierliche Verarbeitung gewährleistet, durch die Sie das Maximum aus Ihren Betriebsabläufen herausholen können.
Doch nicht nur die Palettierer haben sich über die Jahre hinweg weiterentwickelt, sondern auch die Interaktion mit ihnen. Heute ist ein wechselseitig verlaufendes Feedback möglich und Daten können aus der Benutzerschnittstelle extrahiert werden. Informationen über Fertigungsraten, Ausfallzeiten, Wartungsbedarf und Fehlermeldungen können heute viel einfacher gewonnen und analysiert werden.
Konventionelle Palettierer eignen sich hervorragend für lange Fertigungsläufe desselben Produkts. Es besteht jedoch auch die Möglichkeit, verschiedene SKUs mit einer konventionellen Anlage zu verarbeiten. Die Benutzerschnittstelle ermöglicht schnelle und einfache automatische Produktwechsel. Die Steuerung bietet Ihnen gespeicherte Vorlagen mit vordefinierten Einstellungen an, die Sie bei einem Produktwechsel einfach nur auswählen brauchen. Diese Parameter bestimmen, welchem Muster die konventionelle Anlage für eine exakte Palettierung folgt.
Die Eigenschaften der Handhabung können so unterschiedlich sein wie das Produkt selbst. Ob Kartons, Kisten, Gebinde, Ballen, Trays oder eine Kombination aus diesen: der konventionelle Palettierer weiß, wie das Produkt schonend und zuverlässig positioniert werden muss.
Konventionelle Palettierer lassen sich am besten an ungewöhnliche Verpackungen anpassen. Ganz gleich, ob die Produkte besonders klein, groß oder instabil sind – mit einem konventionellen System lassen sie sich alle effektiv palettieren. Dank ständiger technologischer Verbesserungen sind Ihnen in dieser Hinsicht keine Grenzen gesetzt.
WARTUNG
Das Problem ist altbekannt: Ausfallzeiten legen die Produktion lahm. Es wurden allerdings wichtige Fortschritte erzielt, um die Verlässlichkeit konventioneller Palettierer zu verbessern. Dank der Fähigkeit, den Ein- und Ausgangsstatus von Sensoren und Steuerungen direkt am Bildschirm zu überwachen, lassen sich Fehler viel einfacher beheben. Überschreitet ein Maschinenzyklus beispielsweise einen festgelegten Zeitraum oder tritt eine unerwartete Situation ein, so wird dies von Timern oder Sensoren erkannt, die der speicherprogrammierbaren Steuerung (SPS) ein Signal zum Stoppen der Maschine geben. Auf der Benutzerschnittstelle erscheint dann eine Fehlermeldung, auf die schnell zugegriffen und mithilfe derer das Problem behoben werden kann. Die schnelle Übermittlung von Nachrichten auf dem Bildschirm vereinfacht außerdem die präventive Wartung.
Die konventionellen Palettierer von heute benötigen weniger Wartung und wenn sie doch einmal gewartet werden müssen, kann dies in den meisten Fällen von internen Mitarbeiter durchgeführt werden. Sie sind mit weniger Ketten und Kettenrädern ausgelegt, die einer ständigen Überprüfung bedürfen. Wo sich direkte Antriebe als nicht effektiv erweisen, werden Poly-Chain-Riemen bevorzugt, die weniger Instandhaltung und Schmierung benötigen. Die meisten Motoren verfügen über einen variablen Frequenzantrieb, durch den die Geschwindigkeit stufenlos hoch- oder heruntergefahren werden kann. Der variable Frequenzantrieb entlastet nicht nur die Anlage, sondern gewährleistet auch eine schonende Handhabung des Produkts.
Obwohl konventionelle Palettierer aus mehr Teilen bestehen, fallen die Reparaturkosten niedriger aus, da Ersatzteile von lokalen Lieferanten verfügbar sind. Verschleißschichten bestehen heutzutage aus ultrahochmolekularem Polyethylen (UHMW) und nicht länger aus Stahl. UHMW weist eine höhere Stoßfestigkeit und einen niedrigeren Reibungskoeffizienten aus und gleitet damit leichter über metallische Oberflächen.
Die modernen SPS und Benutzerschnittstellen sind über sichere VPN-Verbindungen oder Router mit dem Netzwerk der gesamten Anlage verbunden. Somit kann zur Fehlerbehebung und Wartung per Fernsteuerung auf den Palettierer zugegriffen werden. Ein Lieferant mit einem umfassenden Kundenservice kann Störungen dann gegebenenfalls besser einschätzen.
SICHERHEIT
Im Laufe der Jahre haben sich die Sicherheitsprioritäten in der Fertigungsindustrie verschoben. Früher konnten sich die Bediener der Anlage ohne ausreichenden Schutz nähern. Konventionelle Palettierer verfügen heute über fortschrittliche Sicherheitsfunktionen zur Vermeidung von Verletzungen. Palettierer sind durch Schutzzäune gesichert. Türen und Tore sind mit einer Verriegelungsvorrichtung versehen. Dies gewährleistet eine sichere Abfolge beim Betreten der Anlagenumgebung. Beispielsweise wird der Schlüssel für die Stromquelle auch für den Zugang zu Hochrisikobereichen verwendet. Sobald die Tür geöffnet wird, wird der Schlüssel gesperrt, bis diese wieder geschlossen wurde. Ein Sekundärschlüssel erlaubt dem Bediener Zugang zum eingezäunten Bereich. Die Anlage kann nicht wieder in Betrieb genommen werden, ohne dass sich die beiden Schlüssel in der richtigen Position befinden.
Lichtvorhänge schaffen Sicherheitsbereiche zwischen Mensch und Maschine. Nähert sich eine Person dem Palettierer, wird sie vom Lichtstrahl erkannt und die Maschine wird in einen gesicherten Zustand versetzt. Um die Verletzungsgefahr bei Wartungsarbeiten zu verringern, werden Handläufe auf der Anlage montiert. Außerdem sind Luftablassventile vorhanden, so dass im Falle eines Stopps keine gespeicherte Energie im Palettierer verbleibt.
Konventionelle Palettierer werden mittlerweile mit Sicherheitsbremsen und Wellen ausgestattet, wenn der Betrieb bei laufendem Hebezeug unterbrochen werden sollte. Diese Funktion verhindert unerwartete Bewegungen bei der Wartung oder beim Umsetzen von Paletten oder Produkten im Hebezeugbereich.
Der Kunde hat nun eine bessere Kontrolle darüber, welche Teammitglieder auf verschiedene Ebenen der Anlage zugreifen können. Die Funktionen des HMI-Touchscreens erlauben es nun, Einstellungen vorzunehmen, ohne das Bedienfeld zu betreten. Da ein Wartungstechniker eher Zugriff auf die gesamte Maschine benötigt als ein Bediener, werden für bestimmte Aktionen unterschiedliche Passwörter generiert.
Einige Dinge werden sich bei der konventionellen Palettierung wohl auch nie ändern: Wie bereits in den 1940er Jahren, wird die Ware auch heute noch über ein Zuführband auf den Förderer transportiert und landet letzten Endes auf einer Palette. Auch wenn dieses Prinzip nach wie vor gilt, hat sich die Technologie in diesem Bereich in den letzten Jahren weiterentwickelt, um der ständig wachsenden Komplexität des Marktes gerecht zu werden.
Steigern Sie die Produktivität Ihrer Verpackungslinie
Ganz gleich, ob Sie Ihre Produktionskapazität steigern, ältere Einheiten ersetzen möchten oder die Arbeitsbedingungen – Premier Tech kann Ihnen genau die Anlage liefern, die Ihren Anforderungen entspricht.