Lifeline Foods Setzt Auf Automatisierung
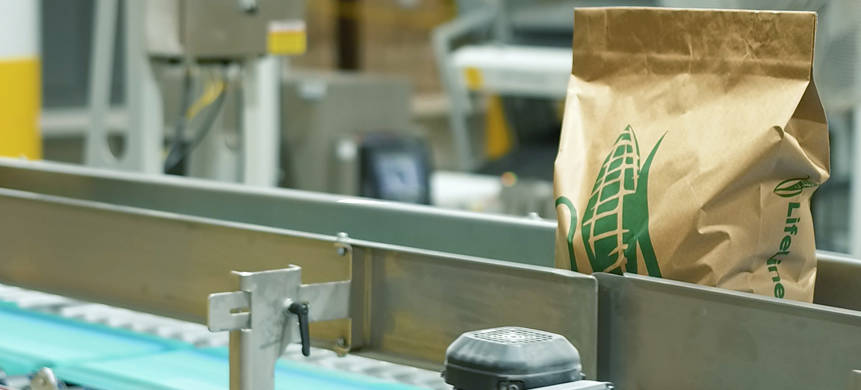
UNTERNEHMENSPROFIL
LifeLine Foods ist eine Erzeugergenossenschaft, die Mais zu Lebensmittelzutaten verarbeitet. Die über 600 Landwirte/Eigentümer stammen aus den US-Bundesstaaten Missouri, Kansas, Iowa und Nebraska und beteiligen sich an weltweit anerkannten, nachhaltigen landwirtschaftlichen Verfahren. Der Betrieb läuft rund um die Uhr, 7 Tage die Woche und beschäftigt 120 Vollzeitmitarbeiter. LifeLine Foods versendet täglich über eine Million Pfund an Lebensmittelzutaten.
EIN FORTSCHRITTLICHES UNTERNEHMEN MIT EINEM VERALTETEN GESCHÄFTSMODELL
Gesteigerte Absatzzahlen sind immer eine gute Sache, nicht wahr? Im Fall von LifeLine Foods machte ein starkes Umsatzwachstum jedoch das Alter des manuellen Verpackungssystems schmerzhaft deutlich. Michelle Clark, Leiterin der Strategischen Planung und Analyse, erklärt: „In einem Jahr stieg die Produktion um 97 %. Wir haben drei verschiedene Anlagen mit unterschiedlichen Sackarten, -größen und Produkttypen betrieben. Wir wussten, dass das kein nachhaltiges Geschäftsmodell war.“
Casey Housman, Operations Manager, sah auch die Nebenwirkungen des Wachstums: Nicht nur, dass die Anlagen veraltet waren, auch ergonomische und qualitative Aspekte, die sich durch eine weitere Nutzung der alten Anlage ergeben könnten, bereiteten dem Unternehmen Sorgen.
Zum Beispiel ließen die Arbeiter die Säcke manuell durch die Versiegelung laufen. „Wenn man das mit 4.000 Säcken pro Tag macht, geht das ganz schön auf die Handgelenke“, so Maschinenbediener Keith Williams.
Gleichzeitig kostete die alte Anlage LifeLine Foods Aufträge. Da einige Kunden des Unternehmens nicht über ausreichend Platz in ihren eigenen Räumlichkeiten verfügten, benötigten sie Paletten, die gestapelt werden konnten. Aufgrund der fehlenden Automatisierung konnte LifeLine Foods die Anforderungen dieser Kunden nicht erfüllen. Mit anderen Worten: Das Unternehmen hätte den Umsatz noch weiter steigern können, aber die alten Anlagen und Prozesse spielten nicht mit.
„Die Ineffizienz und Ungenauigkeit der alten Anlagen hat LifeLine Foods schließlich zur Modernisierung veranlasst“, so Mike Sobetski, ein leitender Angestellter des Unternehmens.
DAS RICHTIGE KNOW-HOW, DIE RICHTIGE BEZIEHUNG
LifeLine Foods brauchte ein Unternehmen mit fundierten Kenntnissen der Branche. Ein Hersteller von Verpackungsmaschinen allein reichte nicht aus. Housman war auf der Suche nach einem Partner, der nicht nur die von LifeLine Foods hergestellten Produkte, sondern auch die für seine Branche besonders wichtigen Anforderungen hinsichtlich Staubentwicklung, Hygiene, Lebensmittelsicherheit und -qualität verstand.
Dank seines Know-hows in der Lebensmittelindustrie konnte Premier Tech Chronos diese und andere Anforderungen erfüllen, um LifeLine Foods während des gesamten Prozesses und sogar danach optimal zu unterstützen. Mike Sobetski: „Die Beziehung zu Premier Tech war bisher sehr gut. Alle Mitarbeiter waren sehr offen, sehr kommunikativ, und unser Anliegen wurde zügig bearbeitet.“
Der Support begann bereits beim ersten Telefonat und begleitete das Unternehmen über den gesamten Weg hinweg bis zur endgültigen Installation. Tim Hale, Maintenance Reliability Projects Manager, sagt, dass das Premier Tech Chronos Team ihn optimal unterstützt habe: Er erhielt Zeichnungen, Bilder und Hilfe, wann immer er sie brauchte.
HÖHERER STANDARD AN ARBEITSSICHERHEIT
Housman freute sich auf die neue Anlage, da LifeLine Foods damit endlich die Ergonomie für seine Mitarbeiter verbessern konnte.
„Nun müssen wir uns um ergonomische Probleme mit Rücken, Schultern, Handgelenken, Händen, Quetschstellen keine Sorgen mehr machen. All das ist in der neuen Anlage sehr gut durchdacht. Die Sicherheitsaspekte der neuen Anlage sind einfach erstaunlich“, so Housman.
Für Housman hat die neue Anlage sowohl die Kompetenzen der Mitarbeiter gesteigert als auch „das gesamte Verletzungsrisiko eliminiert.“
Ein ergonomisches System ist jedoch nur dann sinnvoll, wenn seine Bediener wissen, wie man damit umgeht. Zu diesem Zweck wurden die Mitarbeiter von LifeLine Foods geschult, wodurch die Sicherheit der Mitarbeiter weiter erhöht werden konnte. Sowohl Housman als auch Sobetski schätzten die von Premier Tech Chronos durchgeführte Schulung sehr.
„Die Schulung, die sie von den Technikern vor Ort erhalten haben, war sehr hilfreich und nützlich, und es ist seither zu keinen größeren Zwischenfällen gekommen“, so Sobetski.
Housman stimmt zu. „Die Schulung, die Premier angeboten hat, war großartig. Wir hatten eine beträchtliche Anzahl von Leuten hier, die alle unsere Angestellten geschult haben.“
Premier Tech Chronos war nicht die preisgünstigste Lösung, die LifeLine Foods in Betracht gezogen hatte. Die Qualität der Produkte von Premier Tech Chronos und der Ruf des Unternehmens haben das Projektteam von LifeLine Foods allerdings überzeugt. Housman war vor allem um die Sicherheit der Mitarbeiter und der Verbraucher besorgt.
„Eine schlimme Schulterverletzung, eine schlimme Rückenverletzung und ein Produktrückruf aufgrund mangelnder Kontrolle der einzelnen Schritte – das allein hätte zu größeren Kosten führen können als eine nagelneue Anlage“, sagt er.
SICHERERE UND PRODUKTIVERE ANLAGE
LifeLine Foods hat eine BHS und eine DSR (Waagenzuführsysteme), eine Waage mit dem PTK-1700 darunter, eine Pinch-Top-Verschließanlage, einen AR 225-Roboter und einen hochmodernen Haubenstretcher installiert. Die neue Anlage ermöglichte es dem Unternehmen, die eigene Grundfläche um das Dreifache zu vergrößern, da die Paletten nun perfekt vereinheitlichte Quadrate sind, die gestapelt werden können.
Darüber hinaus haben die neuen Paletten dem Unternehmen geholfen, den Umsatz mit mehreren Kunden zu steigern, wie Houseman erklärt: „Das ist eine ihrer Anforderungen. Manche wollten unsere Produkte nicht benutzen, weil unsere Paletten so schrecklich aussehen und wir sie nicht stapeln konnten. [...] Nun sind wir aber konkurrenzfähig.“
Mit der alten Anlage von LifeLine Foods konnten im Durchschnitt sieben Säcke pro Minute verarbeitet werden. Mit der neuen Anlage konnte das Unternehmen die Kapazität jetzt auf durchschnittlich 14 Säcke pro Minute verdoppeln. Auch Williams ist mit den neuen Anlagen sehr zufrieden. „Wenn wir zur alten Anlage zurückkehren müssten, wäre ich nicht erfreut“, sagt er.
Housman nennt dieses Projekt „das schnellste Projekt, das ich je abgewickelt habe, vom Verkauf, über die Besichtigung der Anlage und den Besuch beim Kunden, bis hin zur Installation. Sie waren mehr als hilfreich. Und sie würden alles in ihrer Macht stehende tun, um einem auf jede erdenkliche Weise zu helfen.“