Was Sie Für Die Entscheidung Zwischen Herkömmlichem Und Robotpalettierer Wissen Sollten
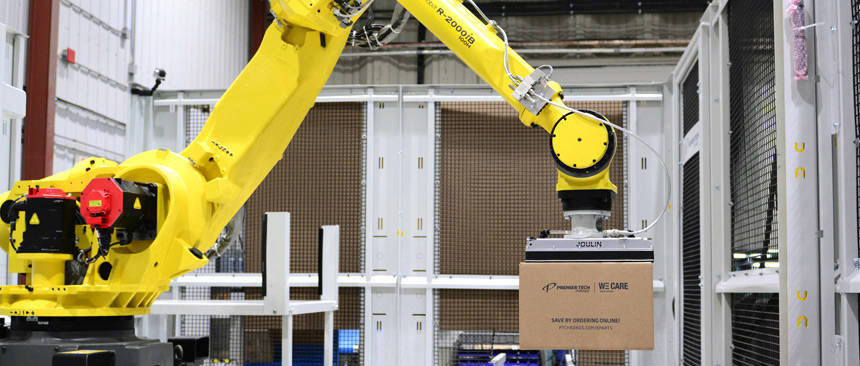
Unternehmen, die sich für die Automatisierung ihres Palettierprozesses entscheiden, haben die Qual der Wahl zwischen zwei Arten von Palettierern: Herkömmliche Palettierer und Robotpalettierer. Sie sind nicht sicher, welche der beiden Technologien für Sie die richtige ist? Hier erklären wir Ihnen den Unterschied, die Vorteile sowie Eigenschaften der beiden Arten und helfen Ihnen, die beste Entscheidung für Ihre Anforderungen zu treffen.
Bevor Sie eine endgültige Entscheidung treffen, sollten Sie genau wissen, was Sie brauchen. Wie viele Produkte verarbeiten Sie? Welche Fertigungsrate müssen Sie erzielen? Diese Fragen helfen Ihnen, sich zwischen herkömmlichen und Robotpalettierern zu entscheiden. Nur wenn Sie sich über diese Punkte im Klaren sind, sind Sie bestmöglich informiert und wissen, was Ihren Prozess optimieren kann.
Um die Plattform auszuwählen, die Ihren aktuellen und zukünftigen Anforderungen am besten gerecht wird, sollten Sie 5 grundlegende Kriterien beachten:
Geschwindigkeit | Wartung | Vielseitigkeit | Stellfläche | Preis
Damit Sie sich einen Überblick über die besonderen Merkmale jeder Plattform verschaffen können, möchten wir Ihnen die beiden Palettierer im Folgenden näher vorstellen.
HERKÖMMLICHE PALETTIERER = GESCHWINDIGKEIT
Lassen Sie uns zuerst einen Blick auf herkömmliche Palettierer werfen, die sich in zwei Unterarten unterteilen lassen: Flachpalettierer und Hochpalettierer. Ein Flachpalettierer verarbeitet Produkte, die auf Förderbändern befördert werden. Diese Produkte werden je nach Palettenkonfiguration ausgerichtet oder rotiert. Sie werden dann gegeneinander gedrückt und formen so eine Reihe. Diese Reihe wird dann von einem Werkzeug, das die Produkte gemäß dem gewählten Muster auf dem Formationstisch anordnet, verschoben oder angehoben.
Die Reihen werden dann eine nach der anderen formiert, bis eine Lage vollständig ist. Der Formationstisch enthält nun also eine vollständige Produktlage und wird gesenkt oder angehoben, bis die Abstreifplatte die richtige Position erreicht hat, um die Produkte behutsam auf der Palette abzuladen. Auf diese Weise entstehen so viele Lagen, wie für eine volle Palette nötig sind. Die Palette wird dann abtransportiert und durch eine leere ersetzt, woraufhin der Prozess von Neuem beginnt.
Bei Hochpalettieren werden die Produkte auch von einem Förderband transportiert, die vollständigen Lagen werden aber nicht angehoben oder gesenkt, um sie auf einer Palette abzuladen, sondern die Palette selbst wird angehoben oder gesenkt, während die Produktlagen fest bleiben. Hochpalettierer erreichen höhere Palletiergeschwindigkeiten und werden in der Regel für komprimierbare Produkte verwendet, da jede Lage auf allen Seiten, d. h. auch oben, komprimiert wird.
Nachdem Sie die Unterschiede nun kennen, kommen wir zu den Hauptmerkmalen und Vorteilen herkömmlicher Palettierer:
- Geschwindigkeit: Herkömmliche Palettierer wurden entwickelt, um unterschiedlichen Produktionsgeschwindigkeiten Rechnung zu tragen. Je nach Modell variiert die Geschwindigkeit zwischen 10 und 40 Säcken pro Minute, kann aber entsprechend der zu palettierenden Einheiten deutlich gesteigert werden (bis zu 200 Kisten pro Minute).
- Wartung: Aufgrund der mechanischen Abläufe ist dieser Palettierer wartungsaufwändiger als ein Robotpalettierer. Die Wartung erfordert jedoch außer Kenntnissen in Mechanik und Pneumatik kein weiteres Fachwissen.
- Vielseitigkeit: Herkömmliche Palettierer wurden entwickelt, um jeweils eine Produktart zu verarbeiten (Säcke, Kisten oder Ballen). Die produzierten Paletten sind im Allgemeinen perfekt und sehr kompakt, da jede Schicht komprimiert und quadriert wird. Mit diesen Eigenschaften lassen sich mit Palettierern dieser Art sehr stabile Paletten produzieren.
- Platzbedarf: Angesichts seiner Funktionen ist ein herkömmlicher Palettierer ein relativ komplexes System, das sowohl am Boden als auch nach oben viel Platz benötigt.
Preis: Vergleichbar mit dem eines Robotpalettierers.
ROBOTPALETTIERER = VIELSEITIGKEIT
Kommen wir nun zu den Robotpalettierern. Das Hauptmerkmal eines Roboters ist natürlich, dass er die ihm durch eine speicherprogrammierbaren Steuerung zugewiesenen Aufgaben eigenständig ausführt. Ein weiterer wesentlicher Bestandteil ist der Greifarm, der für gewöhnlich auf eines oder mehrere Produkte zugeschnitten ist.
Ein Robotpalettierer kann je nach Palettenkonfiguration eine oder mehrere Einheiten gleichzeitig verarbeiten und formt mehrere Lagen auf einer Palette, nachdem er die Produkte von einem Förderband aufgenommen hat. Einer der Hauptvorteile eines Robotpalettierers ist seine Fähigkeit zur Entpalettierung mithilfe eines Sichtsystems. Nachfolgend haben wir die Merkmale und Vorteile für Sie zusammengefasst:
- Geschwindigkeit: Bis zu 40 Säcke pro Minute, wobei nochmals darauf hingewiesen sei, dass die Geschwindigkeit eines Robotpalettierers stark von dem verarbeiteten Produkt abhängt. Es sind zum Beispiel auch Geschwindigkeiten von 1.200 Dosen pro Minute möglich.
- Wartung: Weniger mechanische Bestandteile bedeuten auch weniger Ausfälle und bessere Zuverlässigkeit (geschätzte MTBF: 55.000 Stunden). Das Aufsichtspersonal muss für die Wartung jedoch speziell geschult werden. Premier Tech bietet im Rahmen der Installation der Anlage an.
- Vielseitigkeit: Verschiede Greifarme machen den Roboter sehr vielseitig und gehören zu den wichtigsten Bestandteilen eines Robotpalettierers. Diese speziellen Greifwerkzeuge lassen sich an nahezu alle Anforderungen anpassen. Ob Vakuum, Lateral-, Finger- oder Magnetgreifer: Alle Varianten sind auf die Verarbeitung mehrerer Behälter gleichzeitig ausgelegt, unabhängig von deren Form. Wie oben bereits erwähnt, kann eine Roboter auch zur Entpalettierung der verschiedenen Behälterarten verwendet werden. Verarbeiten Sie mehrere SKUS mit der gleichen Anlage? Sichtsysteme senden Informationen an den Roboter, sodass er verschiedene SKUS auswählen und auf unterschiedlichen Paletten platzieren kann.
- Stellfläche: Die Abmessungen der Anlage richten sich nach der Systemkonfiguration, die Flexibilität ermöglicht jedoch die Installation auf kleiner Fläche bei gleichzeitiger Einhaltung der aktuellen Sicherheitsstandards.
- Preis: Vergleichbar mit dem eines herkömmlichen Palettierers.
Eine automatische Palettierlösung bietet viele Vorteile. Unternehmen bevorzugen diese Technologie für gewöhnlich aufgrund der damit verbundenen höheren Sicherheit und geringeren Personalkosten.
Automatische Palettierer können sich für mehrere Verpackungen und Verpackungsanlagen als rentabel erweisen. Ganz egal warum Sie in Erwägung ziehen, Ihren Palettiervorgang zu automatisieren – eine gründliche Analyse Ihrer Bedürfnisse ist der Schlüssel zur optimalen Lösung.
HYBRIDPALETTIERUNG = DAS BESTE AUS ZWEI WELTEN
Und wie wäre es vielleicht mit einer Kombination der Stärken eines herkömmlichen Palettierers mit denen eines Robotpalettierers? Wenn Sie eine Komplettlösung suchen, mit der Sie Produktüberstand auf der Palette vermeiden können, dann ist ein Hybridpalettierer die beste Option, da hier ein konventionelles Modul mit einem Robotermodul kombiniert wird. Diese Art von Palettierer ist auf die flexible Verpackung (Säcke) ausgelegt und positioniert Gebinde unterschiedlichster Größe auf einer Palette. Die Hybridpalettierung bietet eine gleichmäßige Quadratur und ermöglicht die Palettierung von überhängenden Gebinden.
Steigern Sie die Produktivität Ihrer Verpackungslinie
Ganz gleich, ob Sie Ihre Produktionskapazität steigern, ältere Einheiten ersetzen möchten oder die Arbeitsbedingungen – Premier Tech kann Ihnen genau die Anlage liefern, die Ihren Anforderungen entspricht.