Ventilsackpacker endlich entmystifiziert
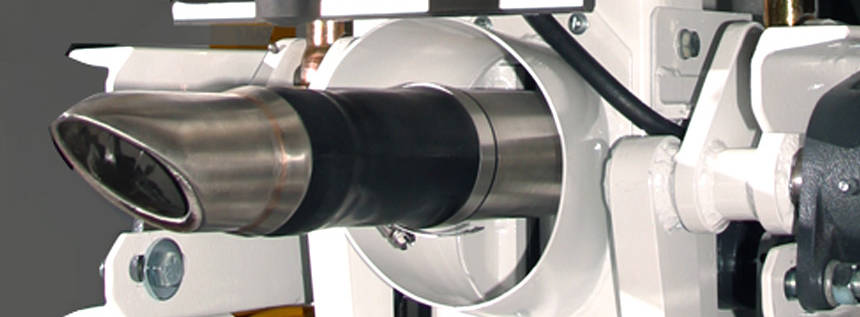
Der Ventilsack wurde um die Jahrhundertwende von Adelmer M. Bates, einem Salzverkäufer, erfunden. Der Legende nach verkaufte er mehr Salz als sein Unternehmen liefern konnte. Seiner Ansicht nach schmälerte die damalige Fülltechnik seine Verkaufsprovision. Als er den Sack entwickelt hatte, gründete Bates sein eigenes Unternehmen, um Anlagen für seinen neuen Sack zu entwickeln. Seitdem haben fünf Maschinen den Markt erobert, mit denen sich eine große Bandbreite an Produkten in Ventilsäcke abfüllen lässt:
- Luftpacker (auch Zwangsdurchlauf genannt)
- Schneckenpacker
- Fallrohrpacker
- Turbinenpacker (auch Gebläse genannt)
- Vakuumpacker
Obwohl sich auch viele Granulate und Pellets in Ventilsäcke füllen lassen, ist diese Art von Säcken bei der Verpackung pulverförmiger Produkte oder Mischungen mit Pulveranteil am weitesten verbreitet. Da die Öffnung eines Ventilsacks viel kleiner ist als die Öffnung eines Offensacks, kann der Strom der pulverförmigen Produkte besser gesteuert werden.
Der erste Vorteil von Ventilsäcken war, dass sie selbstverschließend waren und den Arbeitsaufwand für die Befüllung und das Verschließen (Vernähen per Hand) gegenüber den damals gängigen Offensäcken minimierten. Trotz zahlreicher Innovationen rund um das Ventildesign einschließlich Folienversiegelung und Doppelventil lässt sich mit der Selbstverschlussfunktion bei weitem keine hermetische Versiegelung erzielen. Aus diesem Grund werden viele Säcke in der chemischen Industrie und in der Lebensmittelbranche häufig nach dem Befüllen mit Ultraschall versiegelt. Ventilsäcke bieten außerdem die Vorteile einer größeren Füllmenge und einer rechteckigeren Form, die häufig eine bessere Lage auf der Palette mit sich bringt (verglichen mit anderen Sackformen wie dem Offensack und Form-, Befüll- und Verschließtechnologie).
Der von Bates entwickelte Ventilsack bestand aus Stoff. Die große Mehrheit an Ventilsäcken wird heutzutage aus mehreren Schichten Papier und gegebenenfalls einer Lage Polypropylen hergestellt. Zwar können Ventilsäcke auch aus Polyethylen oder gewebtem Polypropylen hergestellt werden, die Mehrheit besteht jedoch aus Papier.
Von den fünf vorstehend genannten Anlagen werden vier regelmäßig genutzt. Der Fallrohrpacker kommt nur selten zur Anwendung, da er am besten mit Granulat oder Pellets funktioniert und diese Produkte besser mit einer Offensack- oder Form-, Befüll- und Verschließanlage befüllt werden können. Viele der Anwendungsbereiche dieser Maschinen überschneiden sich auch.
Um Ihnen die Auswahl zu erleichtern, finden Sie nachfolgend einen Überblick über die Vor- und Nachteile der übrigen vier Maschinentypen:
Luftpacker (Zwangsdurchlauf)
VORTEILE:
- schnelle Befüllung
- hohe Genauigkeit
- Vielseitigkeit: funktioniert mit feinen Pulvern und Produkten mit einer Partikelgröße von bis zu 3/8”
- keine beweglichen Teile im Produktfluss
- sanfte Handhabung des Produkts – keine mechanische Scherkraftwirkung, geringe Zersetzung
- Einfache Reinigung – Auslassboden und Kammer sind leicht zugänglich
NACHTEILE:
- fügt dem Produkt bei der Befüllung Luft zu
- Risiko, dass ein Sack platzt, da er unter Druck befüllt wird
- weniger geeignet für sehr leichte Produkte (<10 Pfund pro Kubikfuß)
- weniger geeignet für „klebrige“ Produkte (wie Backmischungen mit Fettanteil)
Schneckenpacker
VORTEILE:
- fügt dem Produkt bei der Befüllung wenig Luft zu
- lässt Säcke selten platzen, da der Sack nicht unter Druck befüllt wird
- geringe Anpassungen – leicht verständliche, mechanische Füllmethode
- Vielseitigkeit - geeignet für eine Vielzahl an Produkten, darunter auch für „klebrige“ Produkte wie Backmischungen mit Fettanteil geeignet
NACHTEILE:
- unter Umständen grobe Verdichtung nötig, um Sack fest zu verschließen
- Fluidisierte Pulver können an der Schnecke vorbeifließen, selbst wenn die Schnecke stillsteht
- typischerweise langsamer als andere Befüllmethoden
- wenig Möglichkeiten, die Maschine ideal auf verschiedene Produkte einzustellen
- Abrieb ausgesetzt – Verschleißteile im Produktfluss
- kann mechanische Scherkräfte und Zersetzung des Produktes herbeiführen
Turbinenpacker (Gebläse)
VORTEILE:
- schnelle Befüllung nahezu aller Pulver
- prall gefüllte Säcke
CONS:
- begrenzte Produktspanne – Partikelgröße 200 Mesh und weniger
- schwer zu reinigen (vor Produktwechsel)
- Abrieb ausgesetzt – Verschleißteile im Produktfluss
- kann mechanische Scherkräfte und Zersetzung des Produktes herbeiführen
- Fügt dem Produkt bei der Befüllung wenig Luft zu
- Risiko, dass ein Sack platzt, da er unter Druck befüllt wird
- einige Produkte können zu Wärmeentwicklung im Turbinengehäuse führen – Versengen des Produkts möglich
Vakuumpacker
VORTEILE:
- eignet sich gut für sehr leichte Produkte (<10 Pfund pro Kubikfuß)
- lässt eine pralle Befüllung zu
- sanfte Handhabung des Produkts – keine mechanische Scherkraftwirkung, geringe Zersetzung
- keine beweglichen Teile im Produktfluss
- wenn ein Sack während der Befüllung platzt, bleibt das Produkt in der Vakuumkammer – Umgebung bleibt sauber
NACHTEILE:
- Säcke mit Poylpropylenschicht lassen sich schwer befüllen
- langsame Befüllung
- teuer im Vergleich zu anderen Befüllmethoden
- Säcke können während des Befüllens platzen
Luft- und Schneckenpacker werden oft für Lebensmittel, Chemikalien, Mineralien und einige Futtermittel verwendet. Turbinenpacker werden hauptsächlich für Mineralien verwendet, während Vakuumpacker vornehmlich für Chemikalien zur Anwendung kommen. Obwohl es zunächst ratsam ist, Maschinen zu berücksichtigen, die traditionell für Ihre Produkte verwendet werden, lohnt sich auch ein Blick auf die einzigartigen Vorteile eines bestimmten Maschinentyps. Die meisten Anlagenhersteller bieten Tests an, die Ihnen dabei helfen, herauszufinden, welche Maschine für Ihr Produkt am besten geeignet ist.