Automatisierung des Absackvorgangs durch Nachrüstung von Vakuumpacker
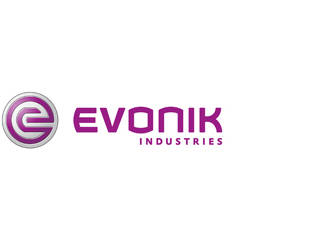
Das Unternehmen Evonik-Degussa mit Sitz in Parsippany, New Jersey betreibt eine Anlage in Waterford, New York, in der hydrophiles (wasseraufnehmendes) und hydrophobes (wasserabweisendes) Siliziumdioxid (SiO2) hergestellt und verpackt wird. Siliziumdioxid findet zum Beispiel bei Farben, Beschichtungen, Klebstoffen oder Silikondichtungsmasse als Füllstoff Verwendung. Es wird in Form von Schüttgut hergestellt und erreicht die Endkunden in Behältern mit einem Gewicht von 10 Pfund bis hin zu Eisenbahnwaggonladungen.
Als die Anlage 1992 die Produktion aufnahm, wurden mittels manueller Vakuumpacker 10- und 20-Pfund sowie 10- und 15-Kilogramm Ventilsäcke aus Papier befüllt. Die manuelle Verarbeitung der Säcke brachte jedoch arbeitsphysiologische Probleme für die Maschinenführer mit sich, sodass sich das Unternehmen dazu entschied, den Verpackungs- und Palettierprozess zu automatisieren und so die Ergonomie der Verpackungsanlagen zu verbessern.
Verpackung und Palettierung von SiO2
Die Geräte der Anlage in Waterford, die zur unternehmenseigenen Abteilung für anorganische Materialien gehört, laufen Tag und Nacht in zwei 12-Stunden-Schichten. Als die Anlage erstmals die Produktion aufnahm, wurde das Siliziumdioxid durch zwei manuelle Vakuumpacker in die verschiedenen Papierventilsäcke gefüllt. Wenige Jahre später stieg die zu produzierende Menge und ein dritter manueller Vakuumpacker fand seinen Weg in die Verpackungsanlage. Der Maschinenführer musste die Säcke manuell in die Absackanlage einspannen und per Hand für die Palettierung vorbereiten.
Mark Honeyman, Betriebsleiter der Abteilung für Wartung und Technik bei Aerosil Silanes NAFTA, berichtet, dass die manuelle Bearbeitung der Säcke an den Absack- und Palettieranlagen Probleme verursachte: „Die Ergonomie der Anlagen und durch Unfälle verlorene Arbeitszeit waren zwei unserer größten Probleme zu dieser Zeit“, so Honeyman. „Ein Maschinenführer, der sich bei der Arbeit am Vakuumpacker unglücklich drehte, musste sich natürlich krank melden. Ein weiteres Problem war die Genauigkeit der Sackabfüllung. Da die Wägeanlagen ungenau waren, konnten die Säcke nicht präzise befüllt werden. Der Maschinenführer, der die Verpackung manuell durchführte, konnte außerdem mit der Geschwindigkeit der Anlage nicht immer schritthalten, wodurch Produktionsstaus verursacht wurden. Honeyman setzte sich mit dem Hersteller der Anlagen, der Premier Tech Industrial Equipment Group (IEG), in Verbindung, um nach einer Möglichkeit zu suchen, einen Vakuumpacker nachträglich mit einem automatischen Sackverarbeitungs- und Verschlusssystem auszurüsten. Die Premier Tech IEG mit Sitz in Rivière-du-Loup, Quebec, beliefert verschiedene Branchen, wie u. a. Chemie- und Pharmaunternehmen sowie die Mineral-, Lebensmittel-, Futtermittel- oder Bauindustrie mit Sackverpackungs-, Zuführ-, Wäge-, Sieb- und Sortieranlagen und hat kurz zuvor den DB-810, eine automatische Sackverarbeitungsanlage mit Ultraschallverschweißsystem, zur Nachrüstung von manuellen Vakuumpackern entwickelt. Das Nachrüstmaterial wurde zur Anlage geschickt und im Oktober 2004 von Honeyman und seinen Technikern mit Hilfe von Fachleuten der IEG installiert. „Nach der Aufrüstung des ersten Packers konnten wir eine Effizienz- und Leistungssteigerung der Anlage feststellen“, so Honeyman. „Auch für die Maschinenführer war diese neue Technik eine Erleichterung, da sie nun weniger Säcke manuell bearbeiten mussten. Im Zuge der Nachrüstung erneuerten die Fachleute außerdem das Wägesystem, was die Füllgenauigkeit und -kontinuität deutlich verbesserte.“
Honeyman entschied sich zwei Jahre später dazu, einen weiteren seiner Vakuumpacker mit dem automatischen System der Premier Tech IEG nachzurüsten. Dieses Mal sollte allerdings auch das Palettiersystem der Anlage automatisiert werden, sodass die durch die manuelle Sackbearbeitung entstandenen Ergonomieprobleme weiter reduziert werden konnten. Honeyman setzte sich erneut mit Premier Tech IEG in Verbindung. Ihm wurde mitgeteilt, dass sein zweiter Packer mit einer verbesserten Version des DB-810 nachgerüstet werden konnte. Evonik-Degussa entschied sich für das aktualisierte System, sodass der zweite Vakuumpacker im Dezember 2006 mit dem DB-815, einem automatischen Sackaufstecker mit Ultraschallverschweißsystem, nachgerüstet werden konnte. Die Palettiereinheit wurde durch die Robotpalettierzelle AR-200 automatisiert. (Eine Robotpalettierzelle besteht aus einem Roboter und Peripheriegeräten, wie Förderbändern, Paletten- und Zwischenlagengebern, die von einem Sicherheitszaun umgeben sind.) Wie bei der ersten Anlage rüstete die IEG das Wägesystem des Packers auf, sodass dieser nun ebenfalls eine bessere Füllgenauigkeit erreicht.
Automatisierte Vakuumpacker und Robotpalettierzellen
Im Grunde funktionieren DB-810 und DB-815 ähnlich, nur dass der DB-810 pneumatisch und der DB-815 elektromechanisch arbeitet. Dank der Nachrüstung der Vakuumpacker muss der Maschinenführer nur noch leere Säcke ins Sacklager laden. Der Rest funktioniert automatisch. „Früher musste der Maschinenführer den Sack vom Stutzen ziehen und das Ventil manuell einfügen, um den Sack zu verschließen“, so Gary Ritter, Sales Manager der Premier Tech IEG. „Dies führte zu ergonomischen Problemen und Produktaufwirbelungen. Die neuen Papiersäcke verfügen über ein externes Ventil mit Kunststoffinnenbeschichtung. Der Kunststoff wird von der Ultraschallverschweißanlage durch Hitze und Druck verschmolzen und ein luftdichter Verschluss entsteht. Die Robotpalettierzelle AR-200 besteht aus einem einzelnen Roboterarm mit zwei Palettieranlagen, von denen jede von einem separaten Förderband mit vollen Säcken versorgt wird. Ein erstes Förderband verbindet den DB-815 direkt mit einer Palettieranlage. Ein zweites Förderband stellt eine direkte Verbindung des manuellen Packers mit der anderen Palettieranlage her. Der DB-810 kann je nach Produkt- oder Sackgröße mit jeder der beiden Palettieranlagen verbunden werden Das Unternehmen verpackt zwei verschiedene Produkte in vier verschiedenen Sackgrößen. Der Palettierer kann so programmiert werden, dass er zwei verschiedene Sackgrößen gleichzeitig stapelt - jede auf eine eigene Palette mit eigenem Stapelbild. Der Maschinenführer muss lediglich die Sackgröße und die Palettieranlage wählen und schon weiß der vorprogrammierte Speicher des Palettierers, wo und mit welchem Stapelbild die Säcke gestapelt werden sollen.
Eine mit dem Palettierer verbundene Kontrollwaage überprüft das Gewicht der Säcke. So kann Konsistenz gewährleistet werden. Das Wiegen findet während der Beförderung des Sacks über die Kontrollwaage statt. Bei falschem Gewicht sortiert ein Roboterarm den Sack aus und transportiert ihn auf ein entsprechendes Förderband. Die Anlage ist so programmiert, dass der Füllvorgang des zugehörigen Packers gestoppt wird, sobald dem Palettierer von einem der Förderbänder kein Sack mehr zugeführt wird. Zusätzlich ist die Anlage mit Sensoren ausgestattet, sodass der Füllvorgang sofort angehalten werden kann, wenn im Verpackungsprozess an einer Stelle ein Fehler auftritt. Dies trägt maßgeblich zur Ausfallsicherheit der Anlage bei. Wenn ein Palettierer beispielsweise sämtliche leeren Paletten aufgebraucht hat, registriert der Sensor dies und stoppt die komplette Verpackungsanlage, da keine weiteren Paletten mehr für die Stapelung der Säcke vorhanden sind. Es werden nur zwei Mitarbeiter für die gesamte Verpackungsanlage benötigt. Ein Mitarbeiter überwacht von einem erhöhten Stand aus die automatischen Packer und stellt sicher, dass die Sacklager noch genügend leere Säcke enthalten. Der zweite Mitarbeiter wird auf Bodenlevel an der Robotpalettierzelle eingesetzt und ist dafür verantwortlich, dass die Lager für leere Paletten und Zwischenlagen gefüllt sind. Außerdem entfernt er volle Paletten vom Stapel.
Optimierung der Absack- und Palettiervorgänge
Seit der Nachrüstung der beiden Vakuumpacker und der Installation der Robotpalettierzelle konnte das Unternehmen eine enorme Produktivitätssteigerung verzeichnen. „Wir haben nicht nur die Ergonomie der Verpackungsanlage verbessert, sondern zusätzlich auch ihre Leistung“, so Betriebsleiter Dr. Hauke Jacobsen. „Im Normalfall können die beiden automatischen Packer jetzt mit der Produktionsanlage Schritt halten. Außerdem haben wir dank der höheren Genauigkeit und Kontinuität der automatischen Befüllanlage präziser befüllte Säcke als vorher. Die Ultraschallverschweißanlage sorgt für einen staub- und leckfreien Verschluss und der Palettierer stapelt die Säcke sehr dicht aneinander, wodurch die Paletten stabiler sind. Ich bin wirklich beeindruckt von dieser Lösung.“
Die Automatisierung der Packer und Palettierer reduziert außerdem die Anzahl der für den Verpackungsprozess notwendigen Mitarbeiter. „Die Maschinenführer haben jetzt mehr Zeit für andere Aufgaben wie Wartung und Inspektionen, weil sie nun nicht mehr an eine einzelne Maschine oder eine einzige monotone, manuelle Tätigkeit gebunden sind“, so Honeyman weiter.