Een verpakkingsactiviteit upgraden met een geautomatiseerde vulmachine en een palletiseerrobot
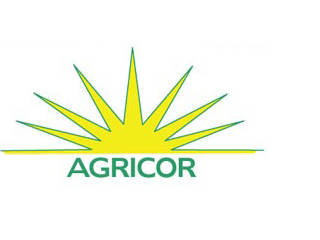
Een graanmolen automatiseert haar vul- en palletisereerlijn om de productiesnelheden te verhogen en arbeidskosten te verlagen. Agricor Inc, Marion, IN, produceert al sinds 1983 drooggemalen graanproducten. Het bedrijf koopt gele maïs van lokale boeren en graansilobedrijven en produceert er maïskorrels zonder kiemen, maïsmeel en bloem van. De producten worden verpakt in bulkcontainers, zoals bulkzakken van 50 en 100 pond en hopperwagons en worden verzonden naar diverse Amerikaanse, Canadese en internationale bedrijven voor gebruik in levensmiddelen en industriële producten. In het verleden vulde het bedrijf handmatig de zakken en palletiseerde deze kleine zakken. Deze methode was echter inefficiënt, arbeidsintensief en stoffig, en dus besloot het bedrijf om te automatiseren.
Verschillende producten verpakken
Het bedrijf verwerkt jaarlijks meer dan vijf miljoen schepels maïs tot korrels, maïsmeel, en maïsbloem. Omdat elk product een andere dichtheid en volume heeft, maakt het bedrijf gebruik van drie formaten 100-pond zakken en twee formaten 50-pond zakken als de verschillende producten in zakken worden gedaan.
Vul- en palletiseerproblemen
In het verleden waren voor het handmatig vullen en palletiseren van de zakken vier tot zes operators per shift nodig, afhankelijk van het formaat van de zakken die gevuld moesten worden. Een operator leidde gevulde zakken door een zakkensluiter, een tot drie operators stapelden de gevulde zakken op een pallet en een operator ruimde eventueel gemorst product en stof op en vulde het magazijn voor lege zakken van de verpakkingsmachine, en een operator reed met een vorkheftruck die volle pallets naar het magazijn.
Bij het handmatig vullen van de zakken en het palletiseren van de verschillende producten kon het bedrijf 100-pond gewone en maïsmeelzakken met een snelheid van 5 zakken per minuut produceren, 100-pond bloemzakken met een snelheid van 3 zakken per minuut, 50-pond gewone zakken met een snelheid van 7 zakken per minuut, en 50-pond bloemzakken met een snelheid van 4 zakken per minuut. Om dit productieniveau op peil te houden en te blijven voldoen aan de vraag van de klanten, moest het bedrijf doorgaans drie ploegen per dag draaien gedurende zes dagen per week, en per ploegendienst een tot twee tijdelijke medewerkers inhuren.
"We hebben eigenlijk met arbeid geprobeerd het productieprobleem op te lossen", zegt Jack Jones, Agricor magazijn en verpakking supervisor. "Voor de 100-pond zakken hadden we een operator voor een machine die bij het palletstapelen hielp. Voor de vijftig-pond zakken hadden we twee operators nodig voor het handmatig stapelen, en in drukkere periodes hadden we wel drie operators aan het werk. Om het risico in verband met het handmatig verwerken van zoveel zakken te minimaliseren, wisselden we tijdens elke ploegendienst de operators bij de vul- en palletiseerstations. Terugkijkend hebben we geluk gehad dat we geen ergonomische problemen hebben gehad toen we handmatig zoveel zakken verwerkten, maar het was altijd iets waar we ons zorgen over maakten."
Steve Wickes, President van Agricor, vertelt dat er nog een ander probleem was, namelijk dat "de vulnauwkeurigheid van de verpakkingsmachines nogal varieerde. Bij de maïskorrels en het maïsmeel kon dat ongeveer een pond schelen met het vastgestelde zakgewicht, en de bloem varieerde aanzienlijk meer dan dat. En aangezien we de zakken meestal te vol maakten, verloren we product bij bijna elke zak die we vulden en dat ging ten koste van onze winstmarge."
Het bedrijf moest haar vul- en palletiseeractiviteiten verbeteren, vooral als het haar het klantenbestand wilde blijven vergroten. "We konden de productie niet verhogen, omdat we de verpakkingslijn al op volle capaciteit gebruikten, dus we verkeerden eigenlijk in een impasse," zegt Wickes. "We moesten ook de nauwkeurigheid van de zakvulling verbeteren om productverlies te minimaliseren, en we moesten het aantal operators en de vereiste tijd voor het vullen van de zakken en het palletiseren verminderen. "Daarom hebben we besloten om de verpakkingslijn volledig te automatiseren en de metaaldetectieapparatuur te upgraden, zodat de productzuiverheid beter gegarandeerd wordt.
Automatiseringsopties
Wickes en Jones namen contact op met verschillende leveranciers van vulmachines en palletiseerapparatuur. "We zeiden tegen hen dat we op zoek waren naar een geautomatiseerde vulmachine, zaksluiter en palletiseerrobot die alle drie de producten kon verwerken zonder dat tijdrovende aanpassingen tussen productruns nodig waren", aldus Jones. "We vertelden hen ook dat de apparatuur voor de verpakkingslijn in een ruimte met een beperkt vloeroppervlak zou worden geïnstalleerd en dat ze de transportlijn en lay-out van de apparatuur waarschijnlijk op maat zouden moeten ontwerpen, zodat alles zou passen in die kleine ruimte. Bovendien moest de verwijdering van de oude apparatuur en de installatie van de nieuwe apparatuur in een zeer kort tijdsbestek geschieden, omdat we ons aan ons productieschema moesten houden. Kortom, de leverancier had slechts twee opeenvolgende weekenden, of ongeveer zesennegentig uur om de gehele verpakkingslijn te installeren."
Onder de concurrerende offertes was er een die zich onderscheidde nadat Wickes en Jones de verschillende elementen van elke offerte hadden bekeken. "We keken naar de kosten van installatie en apparatuur, de kwaliteit van de apparatuur en het systeemontwerp, de filosofie achter het management van het project en de follow-upservice van elke leverancier, en concludeerden dat slechts één leverancier het pakket had dat het meest geschikt was voor onze toepassing en ons budget," zegt Wickes. "Voordat we onze definitieve beslissing namen, stuurden we alle drie de producten naar de testfaciliteit van de leverancier om getest te worden, en we bezochten een van hun installaties in Toronto en spraken met een van hun andere klanten in Saskatchewan. Uit de tests bleek dat hun vulsysteem met gemak onze drie producten kon verwerken, en we kregen uitsluitend positieve feedback van de klanten met wie we spraken, en dus besloten we een geautomatiseerde open-mondvulmachine te kopen met een geautomatiseerde zaksluiter en een programmeerbare palletiseerrobot van de leverancier."
De leverancier, Premier Tech Industrial Equipment Group (IEG), Rivière-du-Loup, Quebec, ontwerpt en produceert op maat gemaakte en geautomatiseerde verpakkings-, palletiseer-, doseer-, en rekfoliewikkelappratuur en -systemen voor de verwerking van droge stortgoederen.
De geautomatiseerde vulmachine en palletiseerrobot
De PTK-1700-serie high-speed vulmachine vult open-mond papieren, PE, en geweven zakken van PP met poeder of korrelige materialen - inclusief mineralen, chemicaliën, voedingsmiddelen en diervoeder - met snelheden tot 25 zakken per minuut, afhankelijk van het zakformaat en materiaal. De oppervlakken van de vulmachine die in aanraking komen met het product zijn allemaal van roestvrijstaal. Daarnaast biedt de vulmachine stofvrije afvulling met totale zakcontrole voor hygiënische en food-grade toepassingen. De machine biedt ook een snelle en betrouwbare overbrenging van gevulde zakken naar het geautomatiseerde zaksluitsysteem.
De PLC van de vulmachine heeft een gebruiksvriendelijk gebruikersinterface in de vorm van een touchscreen, waarmee problemen eenvoudig kunnen worden opgelost, en foutcodes kunnen worden gelezen, en de zelf-diagnostische software biedt noodstopvergrendelingen om de veiligheid van de operator te garanderen als de machine in bedrijf is. Het geïntegreerde weegcontrolesysteem biedt consistent nauwkeurige materiaalwegingen, en het magazijn voor meerdere zakformaten kan snel worden geladen en de zakformaten kunnen snel worden gewisseld.
De AR-200 Serie palletiseerrobotcel kan tegelijkertijd zakken van maximaal vier verschillende productlijnen verzamelen en maximaal 28 zakken per minuut palletiseren, afhankelijk van de eigenschappen van de zakken, de pallethoogte, de lay-outconfiguratie, en andere factoren. Voor toepassing van Agricor had de leverancier de palletiseermachine geconfigureerd om zakken te verzamelen van slechts één productlijn vanwege het beperkte vloeroppervlak.
Een PLC met een gebruiksvriendelijk operatorinterface bevindt zich op de robotcontroller en toont 3D-apparatuur en lay-outtekeningen voor een eenvoudige bediening in de handmatige modus. De interface toont ook opgeslagen aanwijzingen waartoe een operator snel toegang kan toegang voor het wijzigen het zakformaat en het palletiseerpatroon.
De geautomatiseerde palletiseermachine plaatst automatisch lege pallets en slipsheets, en de robotarm heeft een vingergrijper uitgerust met een automatische bag-breedte verstelsysteem. Dit maakt het mogelijk om eenvoudig zakformaten van 9 tot 23 inches breed, 13 tot 39 inches lang en 1,5 tot 6 inches dik en zakgewichten tot 176 pond te verwerken. De PLC van het palletiseersysteem maakt gebruik van een botsbewakingssoftware om schade aan de grijper van de robotarm en andere apparatuur.
Het installeren van de Verpakkingsapparatuur
Het bedrijf huurde lokale monteurs (Industrial Maintenance Specialists) en een elektrotechnisch bedrijf (Rex Collins Electric) in om de nieuwe apparatuur te installeren. Op vrijdagavond 15 februari 2008 begonnen de monteurs, samen met de technici van de leverancier en de operators van Agricor met de verwijdering van de oude vulmachine uit de fabriek. "We haalden de oude vulmachine weg en zetten de nieuwe erin", zegt Jones, "en het volgende weekend installeerden we de palletiseerrobot, de transportbanden en de andere apparatuur. We voldeden beide weekends aan ons installatietijdschema en waren zondagavond producten aan het inpakken. Het was een indrukwekkende prestatie, want alles moest zeer nauwkeurig worden geïnstalleerd, want we hadden geen enkele ruimte over. Tussen de apparatuur en een van de muren is zelfs maar 3 cm tussenruimte. Dat geeft wel aan hoe precies het hele systeem is geïnstalleerd".
Het bedrijf heeft nu slechts drie operators per shift nodig om de verpakkingslijn te runnen: een waakt over alle vulmachines, een maakt schoon, en een rijdt op de vorkheftruck. Het bedrijf vult nu gewone zakken en maïsmeelzakken van 100 pond met een snelheid van 9 tot 11 zakken per minuut, bloemzakken van 100 met 7 tot 9 zakken per minuut, gewone zakken van 50 pond met 15 zakken per minuut, en meelzakken van 50 pond met 8 tot 10 zakken per minuut.
De verpakkingsactiviteiten van het bedrijf verbeteren
Sinds de installatie van de nieuwe geautomatiseerde vul- en palletiseerlijn, heeft het bedrijf haar bedrijfs- en arbeidskosten aanzienlijk verlaagd. "De nieuwe verpakkingslijn verpakt de producten zo snel dat we maar twee shifts per werkdag hoeven te draaien gedurende vijf dagen per week om te voldoen aan onze productieplanning", aldus Wickes. "En de palletiseerrobot heeft onze arbeidskosten verlaagd, omdat we nu niet meer tijdelijke werknemers hoeven in te huren in het drukke seizoen om de zakken van 50 pond te palletiseren. Ook zijn potentiële ergonomische problemen van het handmatig verwerken van zoveel zakken door operators geëlimineerd."
De weegnauwkeurigheid van de vulmachine heeft de winstmarge verbeterd door het productverlies te verkleinen. "We zijn erg blij", zegt Jones. "De nauwkeurigheid van het zakgewicht is zeer goed, en onze klanten zijn tevreden omdat ze precies de hoeveelheid van het product krijgen dat ze bestellen."
Zowel Wickes als Jones waren tevreden met de operatortraining na de installatie en de follow-upservice van de leverancier. "De technici van de leverancier waren zeer goed in het trainen van onze operators op de nieuwe apparatuur en hebben ons echt op snelheid gebracht," zegt Wickes. "En zelfs al is het een enorme leercurve omdat de technologie nog relatief nieuw voor ons is, hoe langer we het systeem bedienen, des te beter we er in thuis raken. Het was ook zeer makkelijk om met de leverancier samen te werken en hij was zeer responsief. Als er iets ooit mis gaat, dan is hun technische support beschikbaar tot tien uur 's avonds. We kunnen ze dus bellen en krijgen dan antwoord over de telefoon, en dat is zeer nuttig geweest."
Dit artikel is bewerkt overgenomen van Powder & Bulk Engineering Magazine, maart 2009