Automation in Powder Packaging: Accuracy Meets Safety
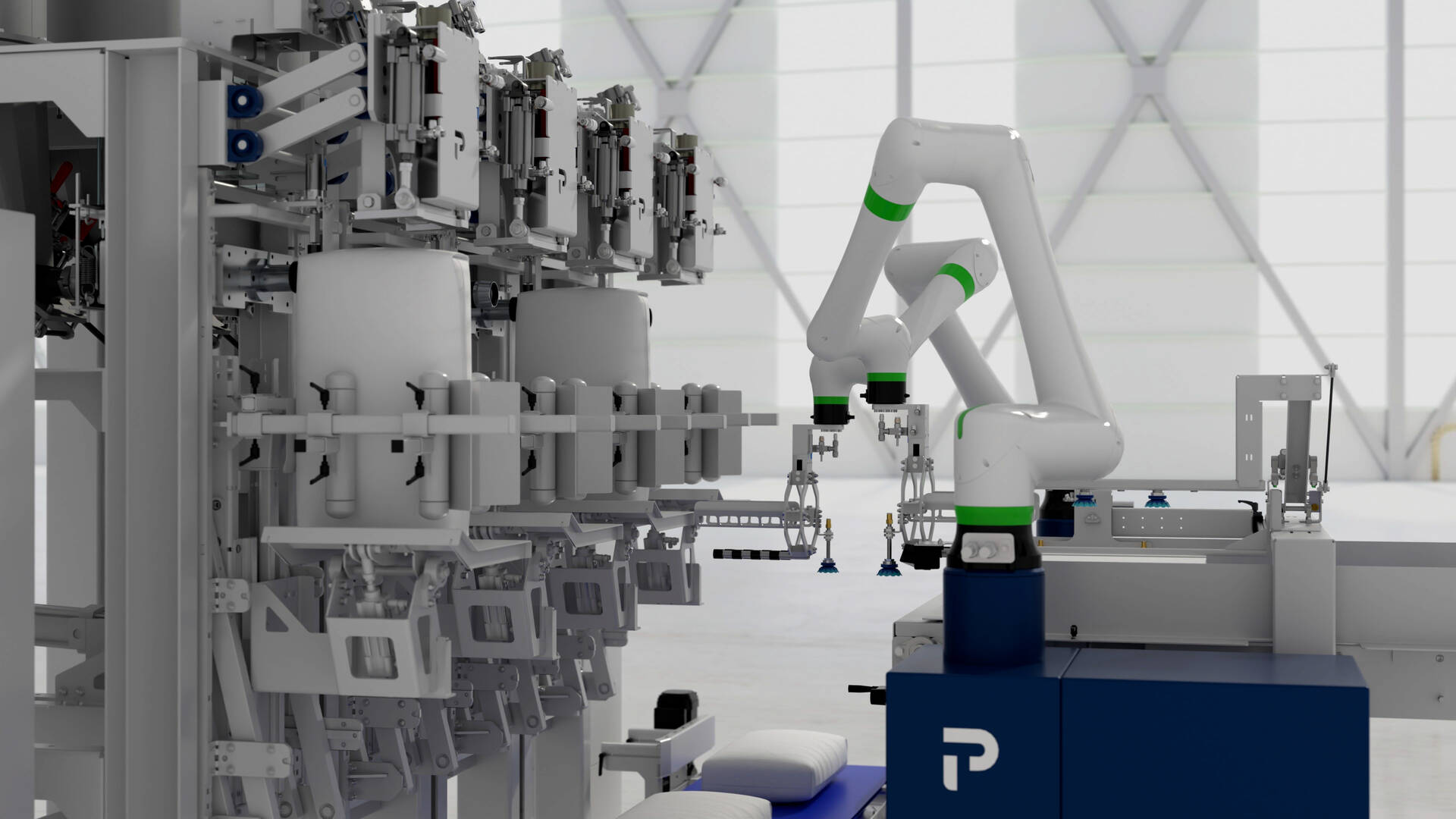
In modern manufacturing, packaging isn’t just about bagging a product—it’s about doing it cleanly, accurately, and consistently. This is especially true for challenging materials like powders, granules, and flakes, which can be sensitive to dust, prone to inconsistent fills, and require careful handling to preserve product quality.
As the industry evolves, automation in packaging has taken center stage. From small-scale operations to large-scale facilities, manufacturers are embracing automated powder filling machines—especially air valve bag filling systems—to tackle key operational challenges and meet growing demand with confidence.
Why product integrity and filling precision matter
Packaging free-flowing or fine materials like powders, granules, and flakes presents a unique set of challenges. These substances tend to behave unpredictably during transfer and filling—creating dust, fluctuating in flow, and often requiring strict hygiene protocols.
Maintaining product integrity and ensuring accurate, clean fills are critical to keeping operations efficient and customers satisfied. Whether you're handling food-grade powders or industrial minerals, automation plays a central role in meeting these goals.
Common challenges in packaging powders, granules, and flakes
Despite their varied consistencies, powders, granules, and flakes often share similar packaging challenges:
1.Dust generation and control
Fine powders can create significant dust during the filling process, leading to material loss, contamination, and potential health hazards for workers. Dust control is especially crucial in food, chemical, and pharmaceutical environments.
2.Filling accuracy
Without precision controls, products may be underfilled or overfilled. This inconsistency can affect product quality, regulatory compliance, and profitability—especially in high-volume production.
3.Product integrity
Maintaining product quality and avoiding contamination is essential. For materials destined for human or industrial use, any compromise in packaging hygiene or sealing can have serious downstream effects.
4.Scalability and flexibility
Manufacturers often need to switch between different product types, fill weights, or packaging formats. Equipment that lacks flexibility or is slow to adapt can become a bottleneck.
5.Maintenance and downtime
Frequent maintenance or unplanned stoppages can seriously disrupt operations, impacting both productivity and cost efficiency.
6.Worker safety
When dealing with airborne particulates or sharp-edged granules or flakes, worker safety becomes a priority. Proper dust control and automated handling help reduce exposure risks and physical strain.
How automation is reshaping powder and granule packaging
To address these challenges, manufacturers are increasingly turning to automated air valve bag filling machines—systems purpose-built for handling powders, granules, and flakes with care, precision, and consistency.
Clean, dust-free operation
Modern systems like the VPF-3000 feature on-spout sealing and enclosed filling environments. This significantly reduces dust escape during operation, improving air quality and minimizing product waste.
High filling accuracy
Automated fillers are designed for tight tolerances, often achieving fill accuracy within ±1 oz. This level of control reduces giveaway, ensures consistency, and helps meet both regulatory and customer requirements.
Hygienic and secure packaging
Machines like the VPF-3000 are available with stainless steel product contact surfaces and ultrasonic bag sealing, helping to preserve product integrity, reduce contamination risks, and support food-grade compliance when needed.
Built for flexibility
With modular design and options like multi-spout configurations and quick recipe changeovers, automated fillers can easily adapt to different product types or bag formats—ideal for facilities that handle varied SKUs.
Reduced downtime and maintenance
Robust components and minimal moving parts reduce the need for frequent service. Some systems offer features like robotic bag applicators that require little to no maintenance for years, improving uptime and reducing operational interruptions.
Improved worker safety
By automating much of the handling process and controlling dust at the source, these systems create safer work conditions, lowering the risk of inhalation and reducing repetitive strain or manual lifting.
Looking ahead: automation as a competitive advantage
In today’s manufacturing landscape, automation in powder, granule, and flake packaging is no longer a luxury—it’s a necessity. Automated air valve bag filling machines help companies reduce waste, maintain product quality, and improve operational efficiency, all while protecting their workforce and preparing for scalable growth.
As packaging demands continue to evolve, automation provides the flexibility and reliability that modern production environments need to stay competitive.
Ready to experience the advantages of automated powder packaging for yourself? Explore the full range of VPF Series bagging machines here.
Ready to elevate your bagging operations?
Optimize your daily operations with our industrial bagging solutions. Learn more today.