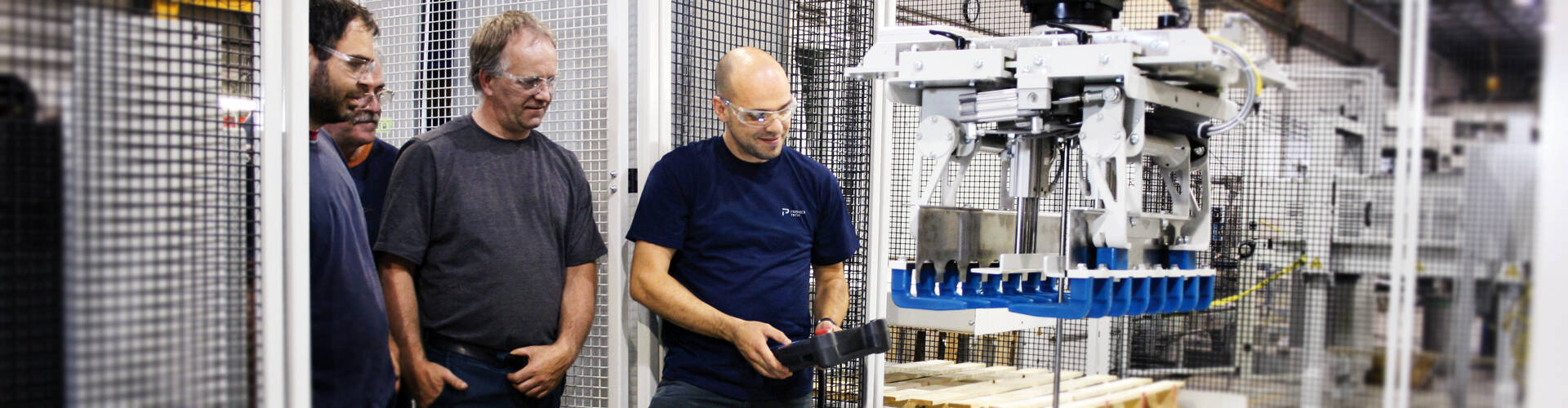
Unlock Your Potential With Our Technical Training Programs
Empower your operation and maintenance teams with Premier Tech's comprehensive technical training programs, designed to build a confident and skilled workforce, leading to optimize operational efficiency.
Online training for seamless onboarding
Address high turnover rates with our plug-and-play virtual training solution, ensure consistent, standardized training for new team members.
Online training for seamless onboarding
Address high turnover rates with our plug-and-play virtual training solution, ensure consistent, standardized training for new team members.
Hands-on training tailored for operational excellence
This program provides customized coaching to maximize equipment efficiency, hosted by an experienced coach-trainer directly at your facility.
Hands-on training tailored for operational excellence
This program provides customized coaching to maximize equipment efficiency, hosted by an experienced coach-trainer directly at your facility.
Maintenance training lab to unlock full potential
This program provides comprehensive knowledge and hands-on experience to troubleshoot and maintain your equipment effectively.
Maintenance training lab to unlock full potential
This program provides comprehensive knowledge and hands-on experience to troubleshoot and maintain your equipment effectively.
Training program comparison
Discover the best training option for you and your team.
Training types | Online | Hands-on | Maintenance lab | |
---|---|---|---|---|
Targeted employees | Operation | Operation & maintenance | Maintenance | |
Delivery method | Online, self-paced | At your operational site | At a Premier Tech facility | |
Expertise level | Beginner | Intermediary | Advanced | |
Number of participants | Individual | Up to 4 team members | Up to 4 team members | |
Duration | 90 minutes per piece of equipment | 1/2 day per equipment (operators), 1 day per equipment (maintenance) | 4-5 days (including one day of virtual training) | |
Languages offered | English, Spanish, French | English, French | English, French | |
Availability by region | North America, Latin America, Europe & Asia | North America, other regions upon request | North America, other regions upon request |
Why choose Premier Tech technical training?
In today’s fast-paced industry, reducing turnover impact and fostering a skilled, motivated workforce are key to long-term success. Premier Tech’s technical training programs are designed to help you build a team that thrives with your packaging equipment.
- Minimize turnover impact
- Boost job satisfaction
- Empower your team
- Achieve operational excellence
Contact us to get started
By investing in technical training programs, you’re not just improving skills—you’re creating a culture of excellence, safety, and commitment.