Don’t Wait for A Breakdown: The Importance of Preventive Maintenance Explained
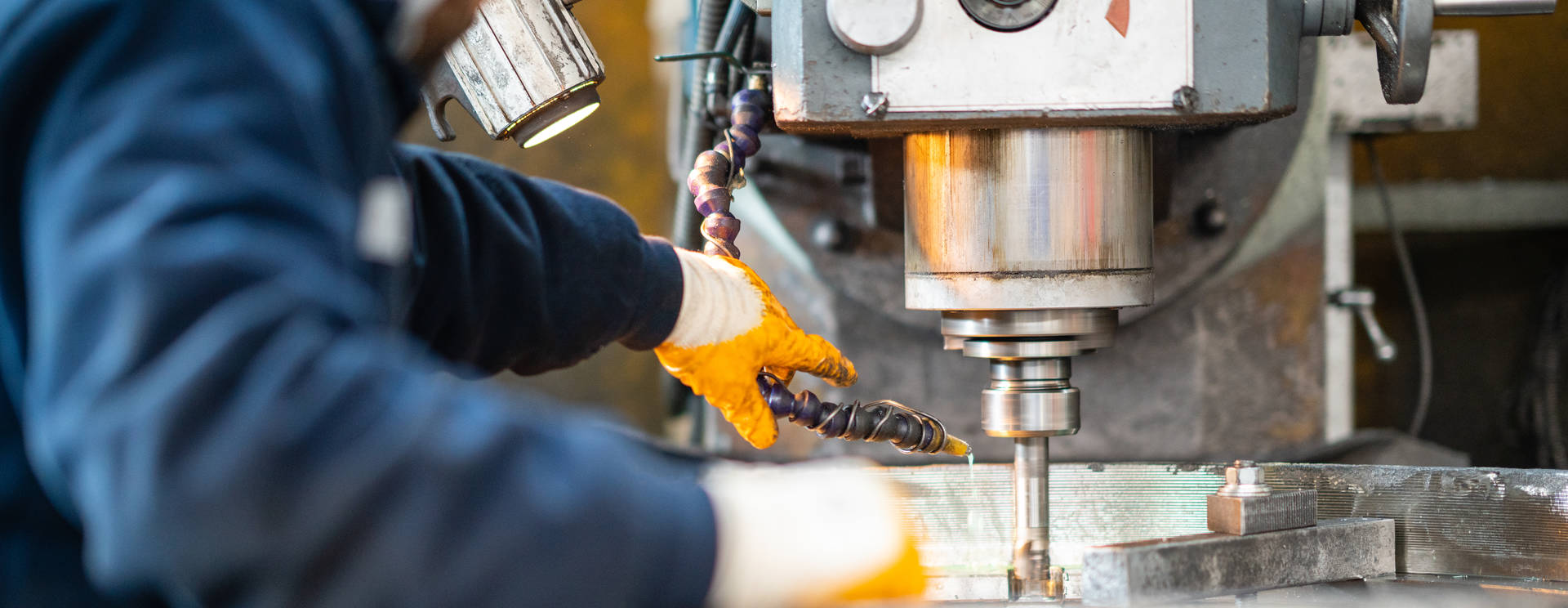
When it comes to industrial packaging equipment, there are generally two schools of thought about maintenance.
One is the reactive approach of fixing equipment only after it has broken down (a fail-based approach). The other is the proactive approach of preventing breakdowns from happening in the first place through preventive maintenance (a condition-based approach).
Think of it this way: would you rather wait until your car’s engine has conked out before getting an oil change, or would you rather give it a regular tune-up and keep it purring like a kitten? The same principles apply to industrial packaging equipment.
In this article, we’ll delve into the benefits of preventive maintenance, and why it beats a reactive approach hands-down. From increased efficiency to higher customer satisfaction, you’ll see how a preventive maintenance strategy can keep your equipment running like a well-oiled machine.
First things first, what exactly is preventive maintenance?
What is preventive maintenance?
In sum, preventive maintenance refers to the routine maintenance of equipment or machinery. It may include regular inspections, cleaning, lubrication, replacement of worn parts, and testing of equipment to ensure optimal functionality.
Preventive maintenance services can be scheduled based on manufacturer recommendations, industry best practices, or an organization's specific needs and requirements.
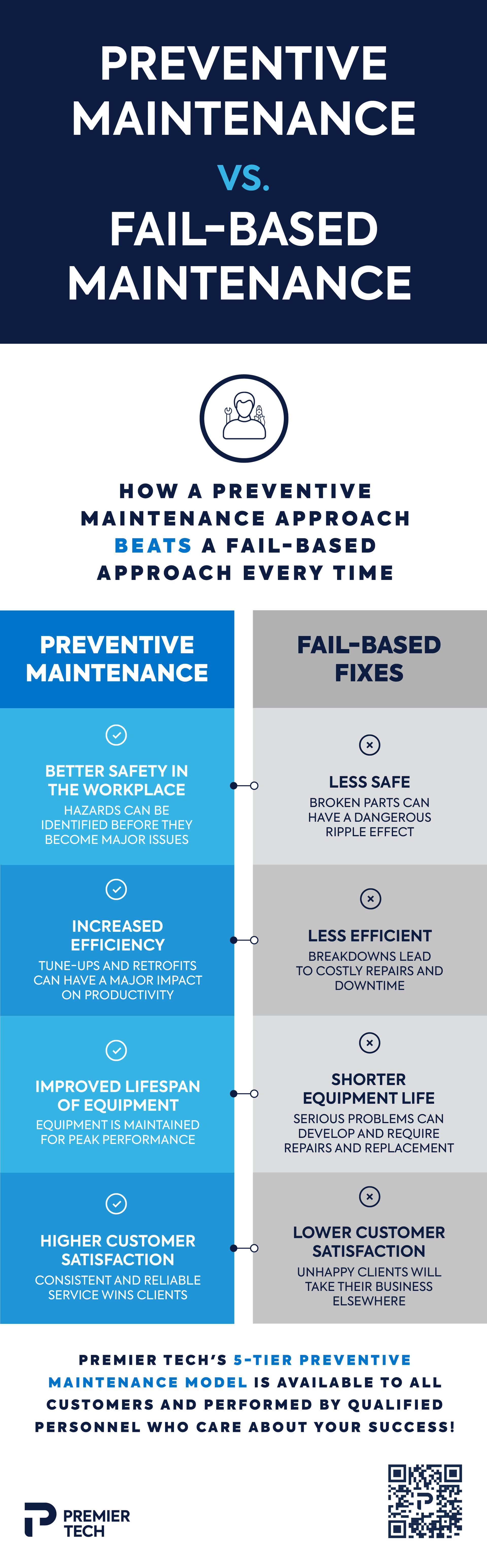
4 Reasons why preventive maintenance is important
Now, let’s move on why a proactive, preventive maintenance approach beats a reactive approach every time namely:
1. Better safety in the workplace
Preventive approach
Preventive maintenance helps to ensure safety in the workplace. Regularly checking on machinery reduces the risk of accidents and injuries and also ensures that equipment is operating within safe parameters.
Reactive approach
In stark contrast, fail-based maintenance can actually increase the risk of accidents and injuries.
When machinery breaks down, it can have a ripple effect, causing other components to become dislodged and creating a significant risk to employees. The sense of urgency created by downtime also tempts employees to get involved in fixing the problem, increasing their exposure to risk.
2. Increased efficiency
Preventive approach
Another significant benefit of regularly maintaining your equipment is increased efficiency.
By checking on and maintaining your machinery on a consistent basis, you can identify opportunities for timely tune-ups and retrofits. These can not only increase production output but reduce the risk of downtime, leading to more profitable operations.
Reactive approach
In contrast, fail-based maintenance can cause significant disruptions to your production schedule. When machinery breaks down, it often requires extensive repairs, which can be costly to complete in terms of time and resources.
Plus, during downtime, production must either be suspended or redirected to other equipment, leading to potential frustrating delays.
3. Improved lifespan of equipment
Preventive approach
Another benefit of preventive maintenance is that your equipment will last longer.
Regular check-ins and tune-ups can help to extend the life of machinery as you can identify and address potential problems before it’s too late.
In addition, regular maintenance can help to ensure that machinery is running at peak performance, reducing unnecessary wear and tear on components and supporting increased business margins in the long run.
Reactive approach
Fail-based maintenance, on the other hand, can shorten the lifespan of equipment. Waiting until problems become serious before fixing them can lead to costly repairs or even the need to replace machinery entirely.
4. Higher customer satisfaction
Preventive approach
Finally, preventive maintenance service can make for more satisfied customers.
By ensuring that your equipment is running smoothly and efficiently, you can provide your client base with consistent and reliable products and services. In this way, preventive maintenance can be seen as an essential part of building a strong reputation and increasing customer loyalty.
Reactive approach
Unfortunately, relying on a fail-based maintenance model risks the exact opposite effect. If customers experience unpredictable delays or interruptions to service, you risk losing their business altogether.
Preventive maintenance in action
Let’s take a quick look at a real-world example of preventive maintenance in action from one of our clients at Premier Tech.
A company we serve in the feed industry decided to try preventive maintenance with Premier Tech through a yearly Service Agreement. After a field service technician went on site to analyze their equipment and ensure it was running at maximum efficiency, these were the results:
Yearly Service Agreement cost: $22,000
Savings generated daily after one visit: $12,000
Payback period: 2 days
In sum, their yearly savings equated to millions of dollars, making their payback period on choosing a preventive maintenance plan only 2 days!
Choose preventive maintenance for long-term success
The benefits of preventive maintenance for industrial packaging equipment are exceptional. By increasing efficiency, improving equipment lifespan, ensuring better safety in the workplace and heightening customer satisfaction, preventive maintenance can help companies reduce costs, improve production and drive long-term business growth.
Get started with preventive maintenance
Premier Tech is proud to offer a five-tier preventive maintenance program to all of our customers, performed by qualified personnel who are invested in your success.
Our approach is designed to prevent and quickly remedy problems and ensure long equipment life, safe operations, and optimal performance.