3 Advantages of a Preventive Maintenance Program and Why it is Essential for Machinery
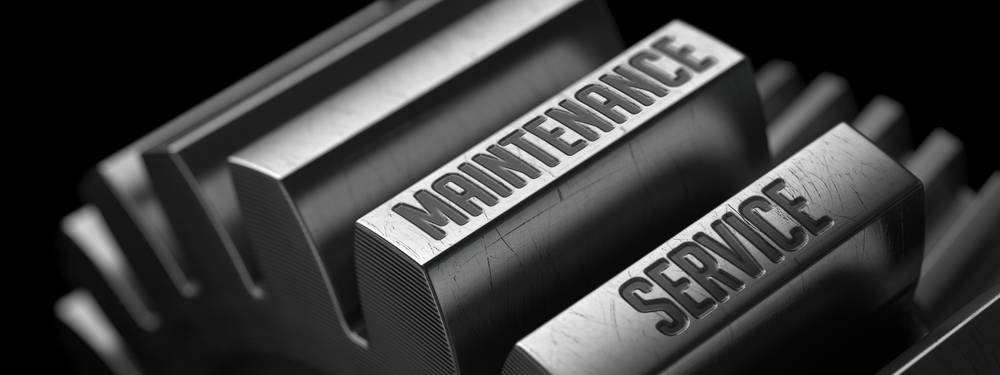
An entire production process from the start to packaging and preparing for delivery, consists of many steps that must happen consecutively. If there is a malfunction in one of the steps, the others will undoubtedly have to stop as well. In a factory setting, where automatic bagging machines must perform tasks quickly to deliver top results, a setback with one machine could cause a domino effect of problems throughout the process.
Therefore, in order for business operators to succeed and bring about results that make their investments worthwhile, their automatic bagging machines must be working at full capacity. Maintaining machine performance so it will be able to work continuously is not only about fixing problems that occur, but about preventing problems from occurring. This can be done with a preventive maintenance program, which reduces the rate at which you must fix or change your machines through regular inspections and maintenance by the technicians.
4 Reasons why Preventive Maintenance is important for Machines
Premier Tech believes that you should prioritize problem prevention with preventive maintenance to preserve machine quality and increase factory capabilities. Below are some of the many advantages to this approach.
1. Save on Maintenance Costs
Many business operators may think that regular condition inspections for the factory’s bagging machines is a waste of time, but compared to getting machines fixed repeatedly, maintenance requires much less time and money. A preventive maintenance program designed for various types of machines, including bagging machines consists of constant condition inspection. If any risk factors are found during these inspections that could cause damage to the machine, the technician will fix it immediately without waiting for the problem to occur, which could take more time to fix, resulting in both a waste of money and a delay in the production process.
2. Machines Work at Full Capacity
After a long period of machine running, it is normal that some parts of a bagging machine may break down. If damaged parts continue to be operated, the machine may not function at full capacity, or there could be setbacks, because parts need to be changed. With a preventive maintenance program, the machine will be checked and maintained its performance. Not only will this reduce the rate of machine breakdown and allow the machines to continue working, but it will extend the machine’s life cycle as well.
3. Be at Ease With Support From our Team
Since the machine system is complex not all operators can properly keep up their systems after the installation. Having a good machine maintenance program ensures that even if there is a problem with the machine, or if another operator does not understand its functionality, you have a local team to support promptly and find the right solution for you. With this program, you do not have to stress about technical issues that you are not familiar with.
4. Confidence in Safety
The most important benefit for preventive maintenance is that it ensures safety when using the machine. Because each scheduled condition inspection considers risk factors and the likelihood of a malfunction, it can help you to avoid mistakes and accidents that could cause property damage or injury to employees.
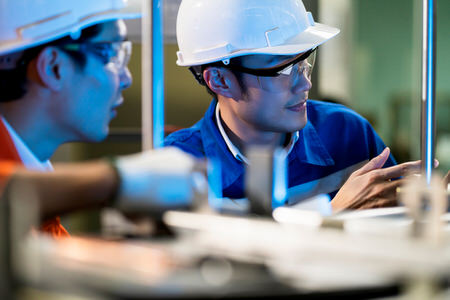
5 After Sales Services that Give Factory Owners Peace of Mind
We had discussions with many business operators on various topics from their problems and needs regarding the machines' operation like bagging machines to the advantages that every factory gains from periodic maintenance services. We have summarized them as five after sales services that lead business operators to success with ease. If you are looking for a new machine to operate, be sure to consider the privileges you will get from each of these services.
1. Technical Call Service
When there are small problems, or you do not understand how the machine works, rest assured because you can consult with our technicians via telephone or LINE Official at any time. You will receive preliminary advice and if you cannot fix the issue yourself, the technician will support you online through VPN system or an AI tool supported by a machine provider to assist customers even over a long distance.
2. Training Service
Switching to an automation system may confuse some operators who are unfamiliar with the machine’s operations, even after post-installation training. Furthermore, when there is a change of operators, new operators may not be familiar with the machine. This is why good after sales services and training programs will be able to keep operators updated with new information and reassured that automatic bagging machines are not difficult to operate with.
3. Field Service
All machine providers should provide a local Field Service Engineer to fix the issue on-site according to the scheduled appointments.
4. Periodic Preventive Maintenance Service
Preventive maintenance service for machines is a periodic service that is undertaken with the mindset that it is better to prevent problems before they occur. Technicians conduct machine inspections and if there are any risk factors, they will suggest solutions or to change parts to prevent any damages in the future.
5. Backup Parts Service Directly from the Manufacturer
Lastly, do not forget to consider machine manufacturers who provide backup parts directly from the factory. This ensures that parts are genuine and can be used with your model of bagging machine. Moreover, if the manufacturer or distributor has an office or warehouse in Thailand, you will receive the parts faster and can continue line production smoothly without any delays.
Business operators who are interested in automatic bagging machines and are looking for partners whose qualifications meet all your requirements, Premier Tech is a great global bagging machine manufacturer to consider. We have years of experience, a local office, and an engineering team in Thailand. We can provide machine preventive maintenance programs and timely after sales services, with all five essential services available to help you complete your production work to the highest level of efficiency.
To read more about after sales service, click HERE