A Quick Guide to Calculating ROI and TCO
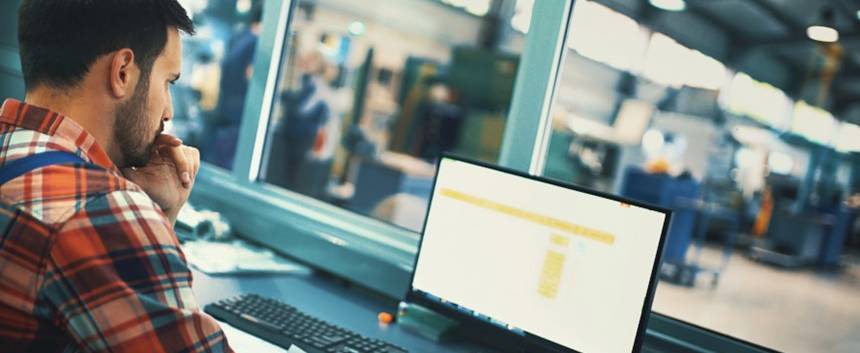
Thinking of investing in new technology for your factory? Wondering how to evaluate the actual value that new machinery can bring to your operation?
Achieving a clear, accurate snapshot of how new packaging equipment such as weighers, bagging systems, case packers and palletizers impact your company is critical when considering a major capital expense - after all, there’s often a lot of money at stake here! Enter two helpful metrics when it comes to assessing your investment: ROI and TCO.
In brief, ROI, or Return on Investment, is the industry standard with regards to capital expenditures and is a helpful way to measure the immediate profitability of an investment.
On the other hand, TCO, or Total Cost of Ownership, is more of a long-term metric that helps determine the total cost of a product or service over its lifetime. It includes not just the initial purchase price, but also ongoing costs like maintenance, repairs and upgrades.
This article will introduce you to the basics of calculating both ROI and TCO and help you understand how these metrics can contribute to knowledgeable decision-making.
How to Calculate ROI
Let’s get started by taking a closer look at ROI. The basic formula for ROI is as follows:
ROI = (Revenue – Cost of Equipment – Operating Costs)/(Cost of Equipment) x 100
So, to calculate the ROI on a piece of equipment, you need to consider the following:
- Cost of the equipment: This is the initial investment required to purchase the equipment.
- Operating costs: This includes all expenses related to running the equipment such as maintenance, repairs, electricity, etc.
- Revenue generated: This is the amount of money the equipment generates in sales.
- Useful life of the equipment: This is the estimated time period for which the equipment will generate revenue.
At this point, you’ll want to analyze the results and compare them to your company’s minimum required ROI threshold or industry standards.
It’s also important to note that ROI calculations are generally based on assumptions and projections. Tracking your actual results and comparing them to your estimations will determine whether your investment is actually meeting expectations.
How to Calculate TCO
TCO is a little more complex as a metric but is worthwhile to calculate as you consider your long-term investment.
To calculate TCO, you need to consider the following costs:
- Initial purchase price: This is the cost of acquiring the equipment.
- Operating costs: This includes all expenses related to running the equipment such as maintenance, repairs and electricity..
- Depreciation: This is the decrease in the value of the equipment over time due to wear and tear.
- Opportunity cost: This is the potential profit that could have been made by investing the money to purchase the equipment in another investment.
- Disposal costs: This is the cost of disposing the equipment when it reaches the end of its useful life.
At this point, you’ll add the costs together to get an idea of the total cost of acquiring and owning the equipment over the course of its useful life. You’ll want to compare the TCO of a given piece of equipment with other options available to determine the most cost-effective solution.
Additional Decision-Making Factors
Upgrading to automated machinery and emerging technologies bring undeniable advantages when it comes to raising your ROI and decreasing your TCO. It’s important to keep some of the following other factors in mind as you make calculations and consider your investment.
For one, consider the increased efficiency that automated packaging machinery brings to the table. Problems like product giveaway, incorrectly sealed bags, micro-stopping and damaged products are virtually non-existent given the right machinery and continued maintenance of equipment. Eliminating these factors will certainly bring down the TCO while increasing profit margins.
Another important consideration is that by automating tedious tasks, you can open up opportunities to reallocate human talent towards projects of greater value. Unlike machines, humans simply aren’t built to perform precise, repetitive tasks 24 hours a day, 7 days a week. Plus, relying on manual labor involves a number of variables and risks that can make it tough to take control of your expenditures. Switching to automated processes can become more of a no-brainer when you think about the impact on ROI and TCO.
Another “X” factor in these equations is the impact automation can have on your ability to recruit and retain new, lucrative market leads. Upgrading your facility by installing new packaging equipment can give your company an edge when bidding for contracts and seeking expansion opportunities. As you estimate your ROI and TCO, keep in mind that having a competitive advantage may wind up proving very profitable over time.
A Real World Example
Here’s a real-world example that demonstrates the benefits of digging deep when calculating ROI and TCO.
A brand-new, bottom-up weighing system for flour gives you the ability to be even more precise on dosing, with a standard deviation of only 20 grams per bag. At a rate of 400 bags per hour, you could save up to $153,600 worth of product per year. Over the typical 15-year lifetime of a weighing machine, this could represent a saving of 2.3 million dollars!
Investing only a fraction of your projected future losses in a new weighing system will not only mitigate product giveaway losses but deliver a host of other benefits to your company (as described above). In this case, the simple math shows that new equipment will pay for itself in as little as two years, while an in-depth analysis can reveal significant profitability long after you’ve recovered the initial capital expenditure.
The Big Picture: ROI + TCO = Your Bottom Line
In sum, assessing the true ROI and TCO of a new packaging project requires careful analysis of a variety of factors as described in this article. Using ROI as a short-term metric and TCO for a long-term overview, you’ll be able to make a strong decision that benefits your company.
Boost your packaging operations
Whether you're looking to increase production capacity, replace older units, or improve working conditions, Premier Tech is ready to respond with state-of-the-art equipment that suits your needs.