- Home
- Products
- Powder Handling Equipment
- Intermediate Bulk Containers (IBC’s)
- Integrated Bulk Container (IBC) system
KOCKUMS
Integrated Bulk Container (IBC) system
Available in
Asia, Canada & USA, Latin America and OceaniaIntermediate bulk containers (IBCs) serve as rigid containers that bridge the gap between drums, sacks, and road tankers.
They come in standard sizes ranging from 0.5m³ to 2.5m³ and can be made of polythene, mild steel, or stainless steel.
Using conventional valves and discharge devices for solids stored in bins may result in incomplete discharge. Our simple and effective cone valve design solves this problem.
IBCs are commonly used in scenarios where cross-contamination and sanitation are major concerns, as in the case of glutens, allergens, flavorings, toxins, and poisons.
Once a recipe is prepared transferring it from a mixer to a packing line can often be an area of concern. Placing an IBC under the mixer (or hopper), allows collection of the complete batch. A telescopic fill spout ensures a sealed connection is made. Once full transfer by forklift truck to the packing line where it can be discharge. Once discharge the IBC can be taken to the wash station. The alternative is to use another conveying method which is not only going to be difficult to clean but will cause downtime too.
The IBC is positioned onto a Discharge station where an actuated probe is located. The probe may be controlled manually or fully automatically and may incorporate custom settings to suit particular product needs. The pulsing action of the probe activates the “CONE VALVE” within the IBC promoting mass product flow, preventing bridges, rat-holes and product segregation. The steep sided smooth conical hopper means that even very sticky materials may be successfully handled. IBC's may be fully or partially emptied leaving minimal in-flight material residue and allowing quick product change over. Direct and accurate metering into process is a common application.
IBC's are supplied complete with an external supporting frame from which lifting is performed. This frame allows safe stacking of the IBC's up to three high minimising floor space and increasing storage capabilities. External tagging, labelling or colour coding of the IBC's assists inventory monitoring, traceability, and sampling. IBC's are fully sealed preventing ingress of moisture and vermin, for short- or long-term storage. They may be used for road transport applications in place of road tankers. Also, product runs may be stored for sample testing prior to final processing or bagging. Nitrogen purging is also possible.
After loading ingredients into the IBC, they may be mixed using a rotating station. The IBC is secured in place and tumbled for a suitable time for mixing to occur. The rotator will be supplied fully guarded to comply with the Safety of Machinery standard AS4024.
IBC's may be a manual or automated process. Both wet and dry cleaning are possible, meeting the sanitary and hygienic expectations of many industries. Fully automated washing and drying stations are also available and include programmable cycles including pre-washing, detergent wash, rinsing and drying.
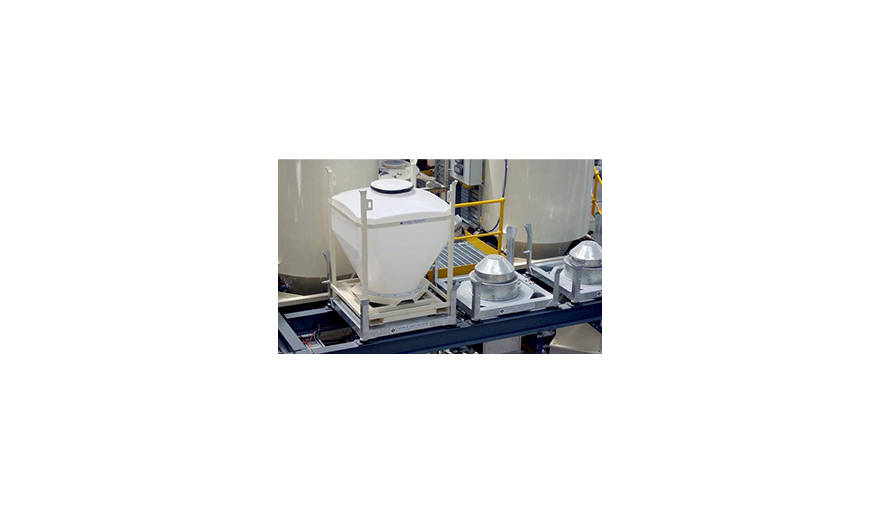
Features
Ability to "pulse" the cone to promote product flow
Capable of metering directly into process
Automated filling and discharging
Stackable for space saving storage
Easy to remove partially empty IBC’s
Poly bottles may be colour coded