Top 10 Most Frequently Asked Palletizing Industry Questions, Answered (2022)
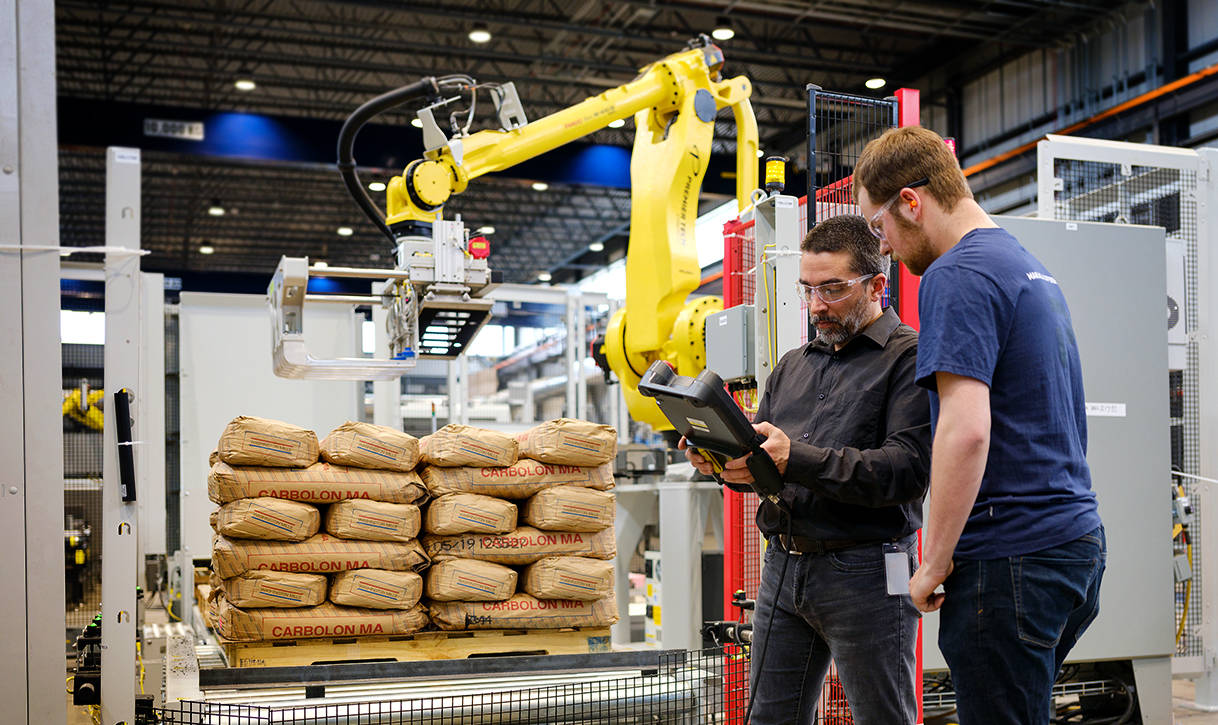
Palletizers have become a staple for many manufacturing businesses around the world. The power and versatility of these machines has revolutionized several industries by increasing productivity while improving safety standards in the workplace. Their characteristics and features allow for a wide array of products to be stacked and shipped more quickly and securely than ever before.
We’ve rounded up the most frequently asked questions we encountered on the web and answered them to create this helpful overview of what palletizing is all about.
Table of contents
2. What is the history of palletizing systems?
3. What are the types of palletizers?
3.1 Manual and semi-automatic palletizers
4. What are the key differences between conventional and robotic palletizers?
5. What arerobot end effectors and end-of-arm tooling (EOAT)?
5.2 Every type of end-effector, listed.
7. What are the benefits of palletizers?
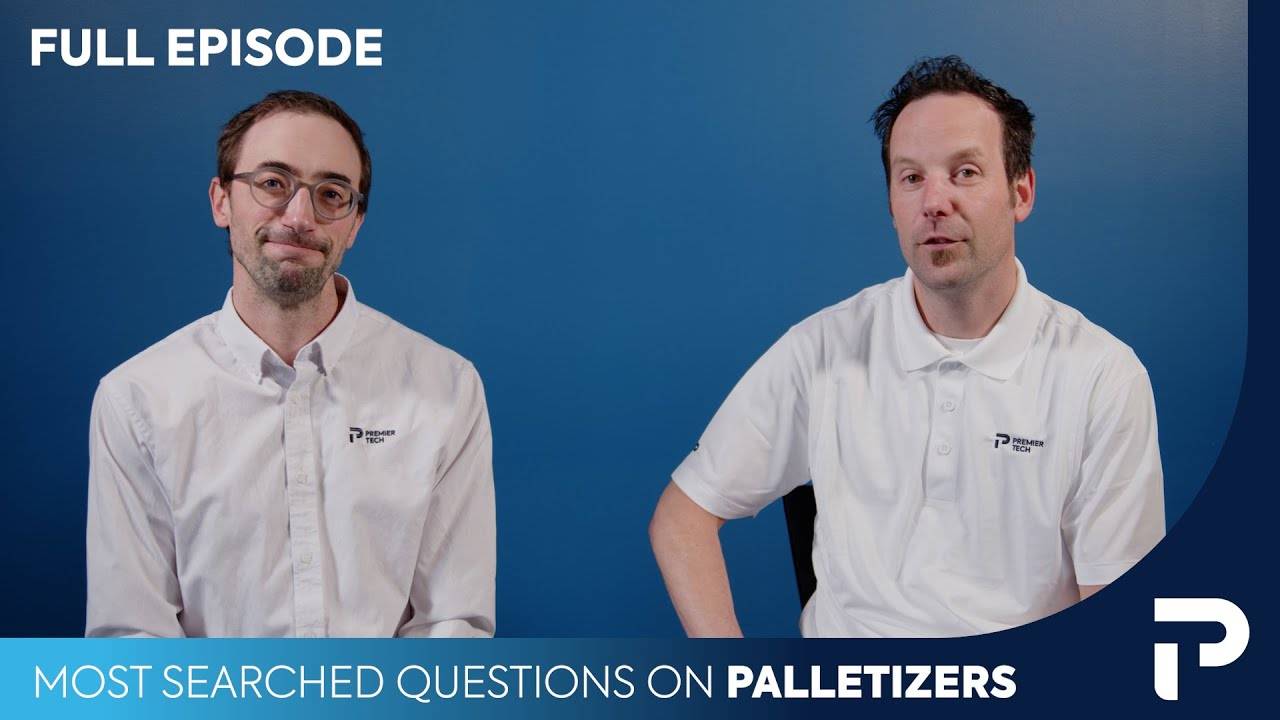
A palletizer is a machine that arranges and stacks products onto pallets in order to create a stable unit load for transportation and storage. The terms palletizer or unitizer may be used interchangeably. That being said, there is a small distinction between the two; palletizers typically place loads on a pallet, while unitizers may place loads on a sheet or directly on a conveyor. Either way, these come in two main functioning methods:
1.1 Conventional palletizers
Conventional palletizers handle products such as bags or cases that are fed into the machine. Units are positioned to create layers and then stacked to create a complete unit load. Conventional palletizers consist of standard components that include:
- A pallet dispenser
- Infeed conveyors,
- Case turners
- Layer-forming tables
- Full load hoist
- Slip sheet dispensers (optional)
1.2 Robotic palletizers
Robotic palletizers function in a similar way with differing components. The key difference is that robotic palletizers utilize robotic arms, which pick up the units and stack them onto the pallets. There are, however, some hybrid models that incorporate both palletizing styles within one machine.
Overall, palletizers are programmed to configure pallet patterns, or in other words, the optimal disposition of products to be well protected and stable during transport or storage. Conventional palletizers specialize in creating cubed loads, whereas robotic palletizers specialize in precise pattern formation. These patterns are programmed into the system and stored as recipes, which can be called up and even edited with a few clicks on a human-machine interface (HMI).
At its core, the palletizing process is the stacking of products to make shipping and storing more efficient. The creation of a well-cubed loads through specific pallet patterns allows businesses to ship more products with less loss due to damage.
2. What is the history of palletizing systems?
Transporting and storing products on pallets became a standard during World War II. Shortly after, in 1948, the first mechanical palletizer was invented for the military by Lamson Corp. This was done in an effort to increase productivity and relieve the physical strain of workers from manually stacking boxes onto pallets. The first commercial palletizer was built for Coca-Cola by George vonGAL, founder of vonGAL Palletizers, in 1957.
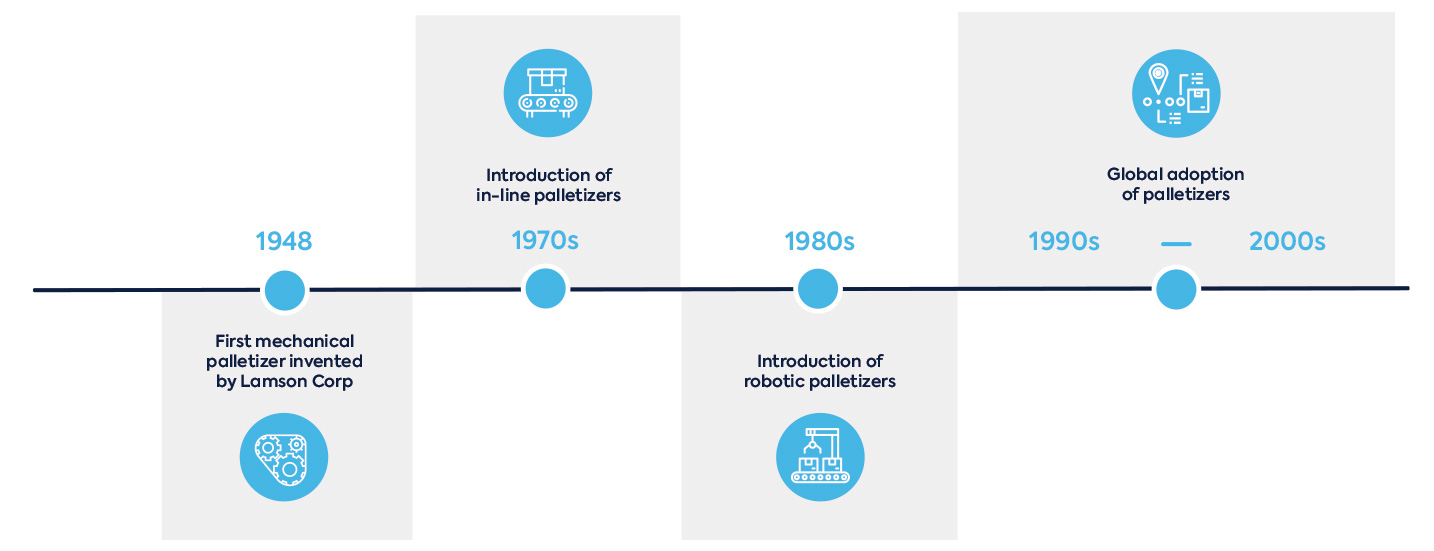
As global shipping started to evolve in the 1970s, demand for enhanced operational efficiency was needed, for which the in-line palletizer was introduced. This machine used conveyors to guide products to a layer-forming table, which then stacked the products onto the pallet.
Then, the 1980s saw the introduction of computers and robotics in the workplace. This innovation brought the creation of robotic palletizers to further increase productivity and precision in the industrial sector.
The 2000s were marked by the high adoption rate of companies acquiring robotic palletizers to meet the rising demand of the market. As more and more industries adopted robotic palletizers to improve their workflow, a variety of end of arm tooling had been invented so that robotic palletizers could solve specific problems.
Conventional palletizers have also evolved over the years and are still very competitive in today’s market. While robotic palletizers have the advantage of precisely forming certain patterns, conventional palletizers have the upper hand in terms of speed and throughput. Either type of system could suit your needs depending on the product being palletized and operational requirements.
3.1 Manual and semi-automatic palletizers - Where it all started
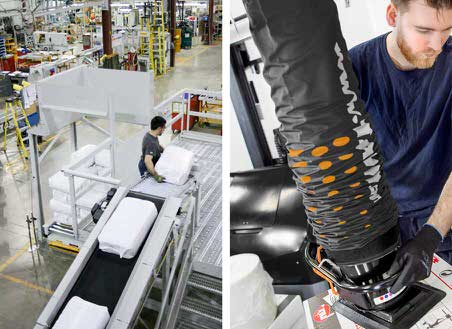
A manual palletizer may simply be moving product by human force or it might consist of a system that helps humans to manually stack products on a pallet. These systems can take the form of a conveyor and pallet lift table or a vacuum lifter. The pallet lift allows the height of the pallet to be adjusted so the operator can easily place each unit onto the pallet.
The second type would be a vacuum-assist lifter. Vacuum lifters are hung from a fixed or mobile metal rack, or hung from the ceiling, using a long tube with a suction cup at the end. This latches onto products gently and securely with a fraction of the normal physical effort it takes to move them to their desired location. The benefit of using this type of system is reducing physical strain and workplace injury.
Manual palletizers represent a cost-effective solution, but there are still limitations in terms of throughput speed and they always require labor.
3.2 Conventional palletizers - The speedy solution
Conventional palletizers are fully automatic systems that receive products (bags, bales, boxes, trays, etc.), form layers and stack them into a unit load. These machines operate very quickly and are suited for a single SKU at a time. Pallet load patterns and configurations are selected on a screen called a human-machine interface (HMI). Current systems may be tied to a warehouse management system to change SKUs and patterns on the fly.
This type of palletizer consists of high performance machines that have the ability to process up to 40 bags or 200 cases per minute. The traditional mechanics of the system means that very little special knowledge is required to properly maintain these machines. Conventional palletizers can produce stable pallets, which save space for warehousing or transit.
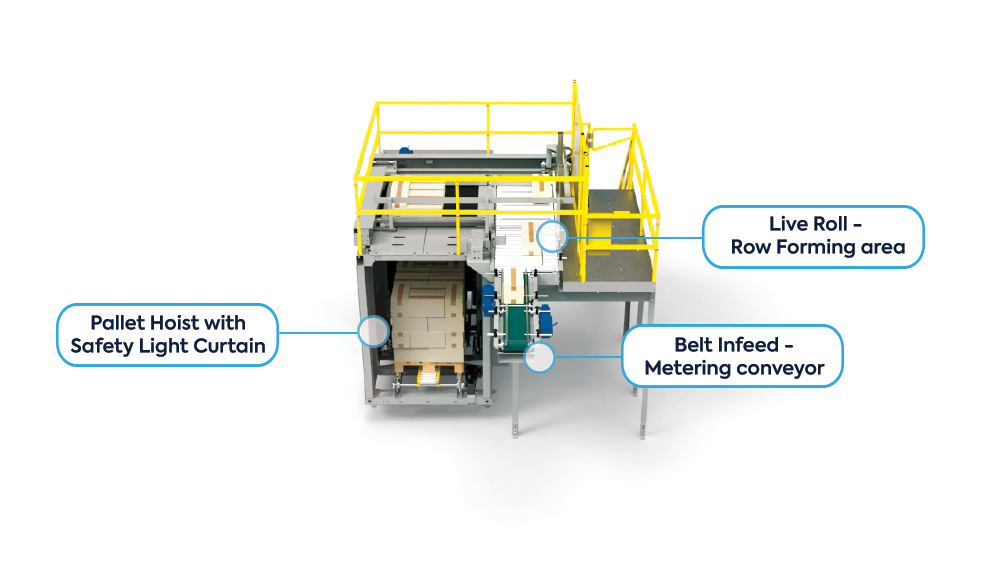
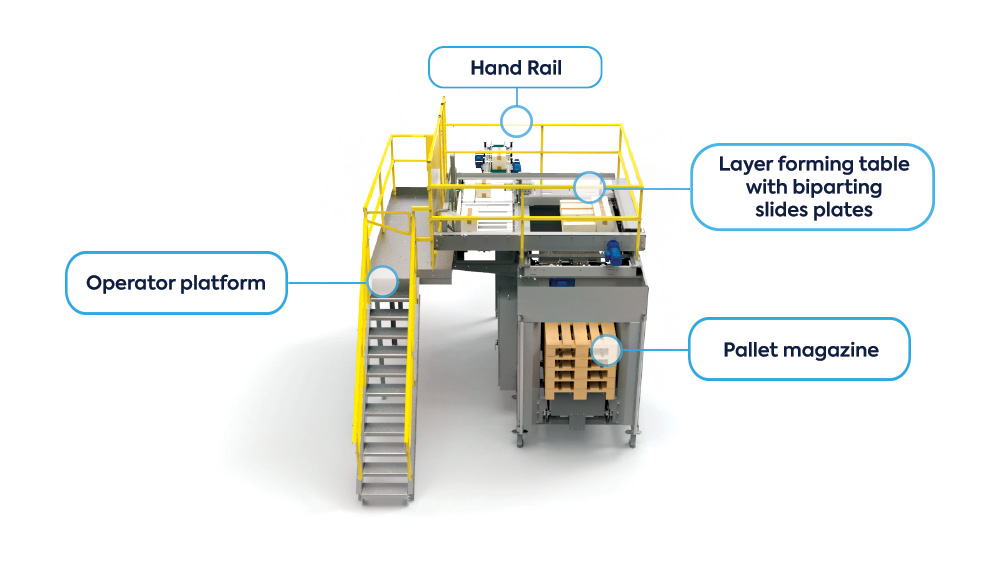
There are two types of conventional palletizers: high-level and low-level systems. The choice between these two options depends on the configuration of your plant and the required throughput.
3.2.1 High-level palletizers
High-level palletizers are fed by a metering belt conveyor with items such as boxes, bags, or trays from the top of the machine; typically seven to eight feet in the air. The operator platform is also located at the top of the machine and the machine’s entire perimeter is secured with hand rails.
The products are arranged in the proper configuration in the row forming area and pushed onto the layer forming table. These layers are formed on an apron that opens over the hoist. The hoist is responsible for raising and lowering the pallet to allow the layers to stack on top of one another. Once the pallet load is completed, it is either picked up by forklift or moved away by conveyors.
3.2.2 Low-level palletizers
The main difference between the high-level and low-level palletizer is the infeed point. While high-level machines typically receive products around eight feet above the floor, low-level machines receive products around three feet above the floor. Rows and layers are built in the same fashion. Once a layer is formed, it is lifted to the top of a pallet and placed as the apron slides away. Due to this extra motion, low-level palletizers are often slower than their high-level counterparts.
Both low-level and high-level conventional palletizing systems offer great reliability and longevity. From a high quality provider, these machines can have up to 99% uptime. In terms of their technical lifetime, some systems remain operational for several decades with proper maintenance.
3.3 Robotic palletizers - The versatile solution
Robotic palletizers use a robotic arm that lifts the products either one by one or in batches, stacking them on a nearby pallet. With this type of process, products can be palletized either one at a time, by row, or by layer depending on the type of end-of-arm tooling. These robots can also be equipped with vision systems to stack products very precisely and even overlap bags.
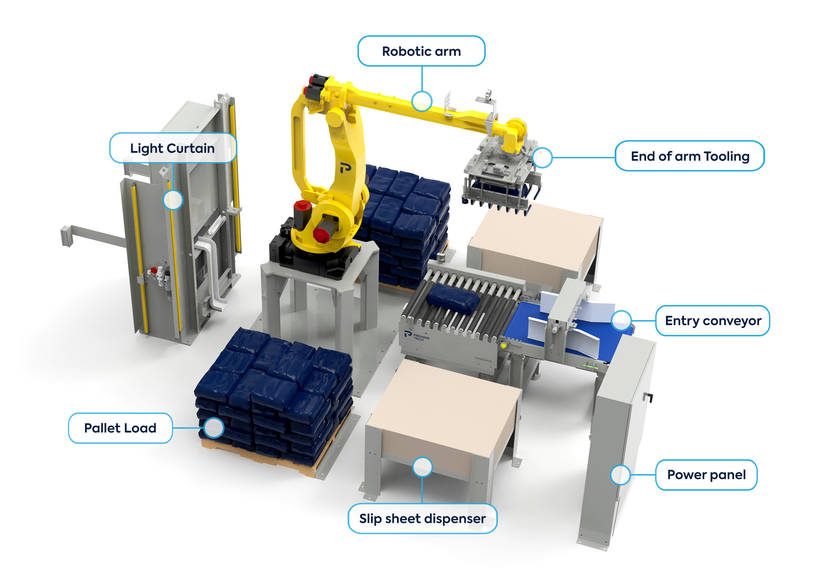
Advanced models can be equipped with a slip sheet dispenser, a pallet dispenser, and an exit pallet conveyor to move the load to the pallet wrapping machine. These features improve the utilization and speed of the machine. Compared to conventional palletizers, they also provide great handling and versatility thanks to the end of arm tooling and software.
Robotic palletizers are also extremely reliable with MTBF (Mean Time Between Failure) rates, reaching up to 80,000 hours. Additionally, they have very short MTTR (Mean Time To Repair) rates. Having both a reliable palletizer supplier and the appropriate spare parts in inventory significantly increase uptime.
Although there is a wide range of configurations of robotic palletizers, here are two examples at each end of the spectrum:
3.3.1 Basic robotic systems
The most basic versions of robotic palletizers include:
- An infeed conveyor
- A robotic arm
- An end-of-arm tooling
- Security fences
Obviously, the entry-level models will have more basic functionalities since they aren’t equipped with slip sheet or pallet dispensers, and the pallet will be located on the floor. Instead of being moved onto conveyors, the pallet would be picked up by a hand truck or forklift and manually replaced. Every time a pallet needs to be replaced, the robotic palletizer's operations must be paused until an empty pallet is replaced.
3.3.2 Fully automatic robotic systems
Fully automatic palletizers come with:
- An infeed conveyor
- A robotic arm
- An end effector
- A pallet dispenser
- A slip sheet dispenser
- Security fences
The palletizing process begins with an entry conveyor, which carries the products to the robotic arm while the pallet dispenser carries an empty pallet to the palletizing station. Then, the slip sheet dispenser layers a sheet over the pallet for the robotic arm to load the items. Once the empty pallet and the slip sheet are in place, the robotic arm starts picking and placing the items from the entry conveyor to the pallet until the pallet is fully loaded.
The exit conveyor moves the loaded pallet towards a stretch wrapping station. A forklift is then used for storage or transit, after which the process starts all over again. A great benefit of the fully automatic robot palletizer is that the pallet magazine can be refilled without stopping the system’s operations.
Some automatic palletizing systems replace the standard robotic arm with a cobot, which stands for collaborative robot. Cobots collaborate with plant staff instead of substituting them. Cobots add great value to a palletizer because it increases safety for all the employees surrounding the palletizer, as there are sensors in the arm that detect whether any people or objects are in its surroundings.
The main benefit is that cobots enable staff to work alongside the machine safely and maximizes floor space. It removes the need for any security fencing around the palletizer. The main disadvantages of Cobots compared to the standard robotic arms is in terms of efficiency. They have significantly lower weight capacities and do not operate as quickly.
3.4 Hybrid palletizing - Great for specific applications
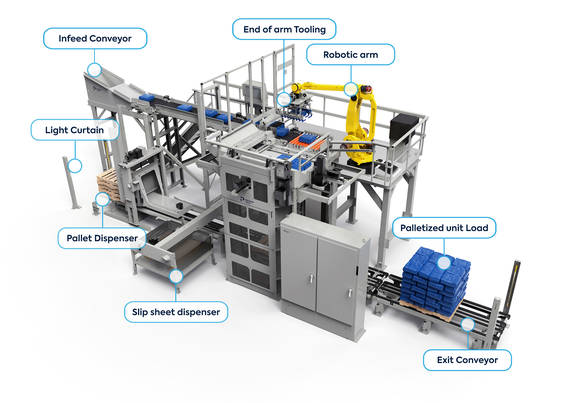
Hybrid palletizing refers to the combination of high-level conventional and robotic palletizers on a single production line to achieve a custom palletizing process. The hybrid palletizer will generally utilize robotic arms to feed a conventional palletizer and form layers. Once the layer is formed, the apron on which it sits releases the load onto the pallet hoist. Finally, the palletized unit load moves along the conveyor to be wrapped, stored or transported.
Hybrid palletizers are best for certain scenarios where a customized option is required. For instance, if the required throughput rate for your operation’s needs is significantly higher than what robotic palletizers offer, then the hybrid variety may be for you. If overlap is required for the products you are palletizing, that would be another great reason to opt for a hybrid palletizer.
4. What are the key differences between conventional and robotic palletizers?
Conventional and robotic palletizers share some common utility, while also having their own distinct use cases and advantages. They vary in terms of:
- Versatility in the types of products handled
- Productivity
- Maintenance requirements
- Safety
- Cost
- Floor space
The table below compares the capabilities of both conventional and robotic palletizing systems:
![]() | ![]() | |||
---|---|---|---|---|
Conventional | Robotic | |||
![]() | Products Handled & Versatility | Handles 1 SKU at a time. Adapted for cases, bags, bales, trays, etc. | Handles 1 or multiple SKUs at a time. Adapted for virtually any type of product. | |
![]() | Productivity | Cases: up to 200/min Bags: up to 40 per minute | Cases: Up to 80/min. Speed varies depending on the configuration and quantity of products handled per pickup. Bags: Up to 40/min | |
![]() | Maintenance & Training | Slightly more maintenance, less training required | Slightly less maintenance, more specialized training required. | |
![]() | Safety | Trapped key interlocking Fences Light curtains etc. | Trapped key interlocking Fences Light curtains etc. | |
![]() | Cost | $-$ Price varies mostly depending on the speed of the equipment | $-$$ Price varies mostly depending on the level of automation, the type of product handled, and the speed. Custom solutions are available and tend to be more expensive. | |
![]() | Footprint | Slightly smaller footprint than equivalent robotic systems. | Slightly larger footprint than comparable conventional palletizers, compensates with modularity. |
5.1. What is an end effector?
End-of-arm-tooling (EOAT), also known as end effectors, refers to the various tools that can be installed at the end of a robotic palletizer arm. They allow the machine to handle:
- Bags
- Jugs
- Cases
- Trays
- Bottles
- Cans
- Bales
- Bundles
- Pallets
- Totes
End effectors can be swapped out to do multiple jobs and are often made for specific product types or situations. Let’s look at the most common types that are used.
Clamp gripper (Bundle gripper)
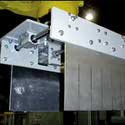
A clamp gripper uses metal plates to press either side of the bag or box to lift it.
Finger gripper
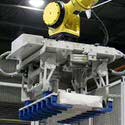
A finger gripper lifts products via tines that slip under the packaging from either side. This EOAT is very common for bags as it can easily handle various sizes with a few quick adjustments.
Fork gripper (Lateral finger gripper)
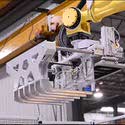
Fork grippers are used mostly for oversized bags and open-top boxes that must be lifted from the bottom.
Magnetic gripper
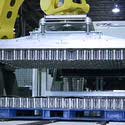
As its name implies, this gripper uses strong magnets to pick up metal products like cans or building materials. This ensures they’re carried safely without the risk of scratching or denting the products.
Pail gripper
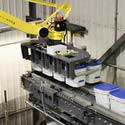
As the name implies, this gripper is made specifically to pick up pails by the lip under the top of the container.
Ring gripper
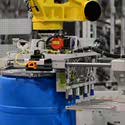
This circular tool is explicitly used for drums and other round containers to lift them from the top to carry them.
Pallet & slip sheet gripper
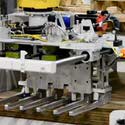
This tool is generally added to a regular gripper to make it more versatile and able to handle pallets, slip sheets and loose products. This option is valuable for operations without a pallet and/or slip sheet dispensers.
Vacuum gripper
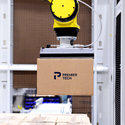
This gripper uses vacuum technology to pick up products gently and safely. This tool is primarily used for products that can only be lifted from the top.
6. Types of pallets
Pallets come in a variety of shapes and materials, and choosing the correct one is an important aspect of the palletizing process. Here are the most common pallet types in the industry:
6.1 Pallet styles
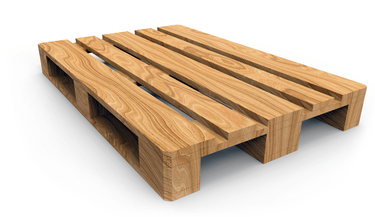
6.1.1 Block pallets
These pallets have four points of entry so forklifts can use them from all sides. They can be made out of wood, plastic or plywood and they get their name from the 9 blocks of material that form the structure of the pallet.
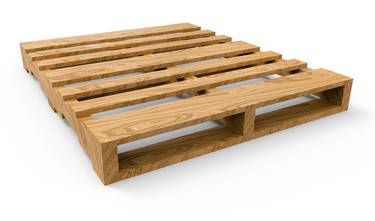
6.1.2 Stringer or GMA pallets
These pallets get their name from the 3 planks of wood that hold the slats. Stringer, or GMA pallets, may be designed as either two-way or four-way pallets, depending on whether or not they have notches. You may also see some where the top boards extend past the stringer. These are referred to as Winged-Pallets and are primarily used in the military.
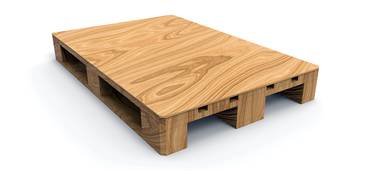
6.1.3 Solid deck pallets
These pallets don’t have slatted tops, but instead, have a full square of plastic or wood, sometimes with small openings to allow for drainage. They are often used for products that don’t need the aeration or drainage of a regular pallet, but instead require added protection.
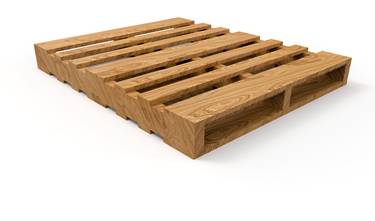
6.1.4 Double-faced pallets
All the previously mentioned pallets can come in a double-faced version. This simply means they have slats positioned across at the top and bottom of the pallet, whereas a regular pallet only has slats on one side. This design allows for more versatility and speed since the pallet can be used from either side and no time is wasted flipping it into position. This also makes the pallet much more structurally sound for heavier loads.
Pallet sizes
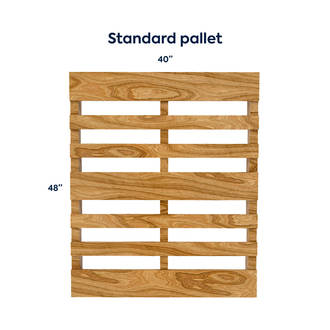
Standard pallet 48’’ x 40’’
This is the standard pallet type across North America and comprises 30% of the market. It has dimensions of 48 x 40 inches and a safe working load of up to 4,600kg
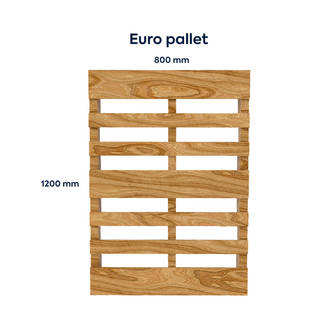
Euro pallet 1200 x 800
This pallet style is the standard across European countries, it’s a 4-way pallet in a rectangular shape with dimensions of 1,200 mm × 800 mm × 144 mm and a safe working load of 1,500kg
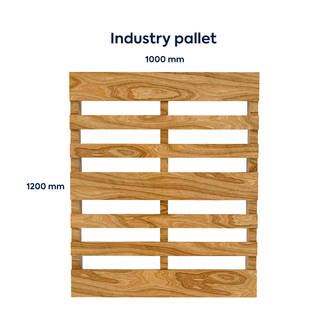
Industry pallet 1200 x 1000
Another common pallet size in Europe used for larger loads.
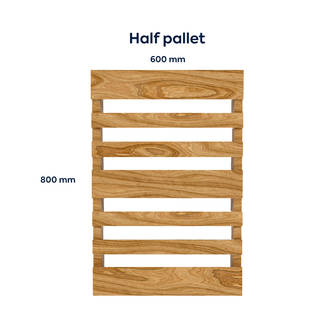
Half pallet 800 x 600
This type of pallet is used for smaller loads that wouldn’t fill a full pallet but still need to be shipped. They follow the standard of a pallet in their region, which means in North America a half pallet is 40 x 24 inches and 800 x 600 mm in Europe.
7. What are the benefits of palletizers?
The advantages of palletizers:

1. Efficiency
The throughput is incomparable to manual solutions, as palletizing machines can process up to 200 units per minute. A palletizer with proper maintenance can run 3 shifts a day for many decades and achieve very high production rates throughout its life.

2. Safe workspace
Loading pallets manually is strenuous work that is inherently dangerous to the human body if done long enough. Using a palletizer to load products gives your employees a better quality of life and reduces the risk of injury by reducing repetitive movements.
Most palletizers are equipped with safety features such as light-curtains at entry and exit points that trigger the machine to stop if an object is detected. Trapped key interlockings, which are a series of locks placed on palletizers, require a key to be removed from the HMI and placed in the gate lock in order to operate specific portions of the machine. This ensures operators are kept safe and unable to access dangerous areas while the palletizer is in motion.

3. Unit load consistency
When palletizing is done by a human, there’s a higher margin of error than a system that has been programmed to execute the task at hand. The consistency of conventional or robotic palletizers allows them to produce loads that are compact, shaped, and stable. Properly palletized loads reduce damaged products during transportation within the plant or during shipment.
8. What is a unit load?
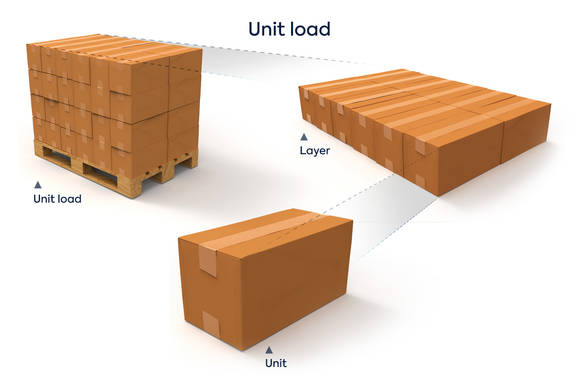
A unit load is a set of items such as boxes, trays, or bags, that are set and wrapped onto a pallet or slip sheet in various patterns. It ensures stability, even weight distribution, and the smallest possible footprint with the purpose of being handled as a single unit for warehousing or transit. The unit load may be wrapped manually or automatically by a stretch wrapping machine or a hooding machine.
A palletized unit load consists of 4 core elements:
- Unit: A single item such as a bag, box, bale, jug, tray, etc.
- Row: A set of items configured in a straight line.
- Layer: A set of rows side-by-side and parallel to each other forming a layer.
- Unit load: Layers that are stacked on top of one another in varying pattern configurations and then stretched wrapped, forming a new single unit.
The three most common pallet patterns are brick, pinwheel and block. Brick and block are mostly used for cases, while pinwheel patterns are more often used for bags. These patterns not only provide more steadiness to the load, but also ensure the products remain in an efficient square shape and under the height requirements of transporters to fit in trucks.
Let’s take a look at each unit load pattern type
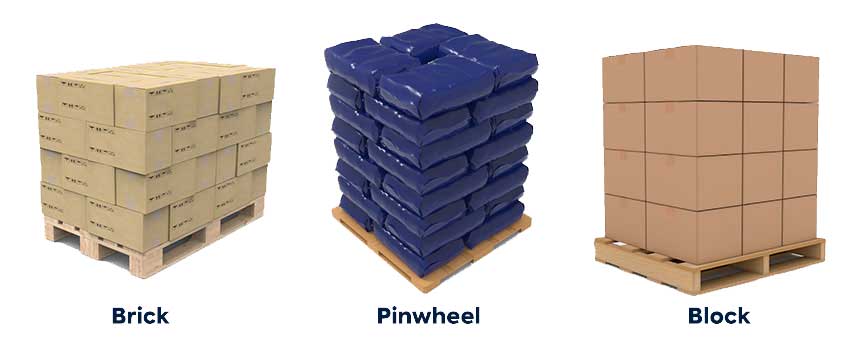
- Brick or interlocked: The units are placed in parallel along the edges and perpendicularly at the corners of the pallet, continuously until the layer is filled, creating a circular brick-style layout. The brick method is also very space efficient, having no gaps and is extremely stable as the boxes are facing different directions, reducing the overall risk of them falling.
- Pinwheel pattern: The individual units, or sets of 2-3 depending on the size, are positioned perpendicular to one another in the form of a pinwheel. The pinwheel method is used for boxes, but more often bags, especially when four is the ideal number for the layer. Bags benefit from this because they are soft and their dimensions can slightly vary in shape, making the pinwheel a desirable arrangement. This pattern is very stable because the units are facing different directions, reducing the chances of slippage.
- Block or column pattern: The units are uniformly stacked with one another, perfectly aligned both horizontally and vertically. Boxes stacked with the block pattern method are extremely space-efficient and are relatively stable so long as the weight of the units are equal.
Here are some tips to avoid in terms of patterns and unit load:
- Avoid creating a palletized unit load with a pyramidal shape, because the unit distribution will be uneven, creating an unstable load with high risk of the items in the upper layers falling.
- Minimize gaps to not only maximize space usage, but also to reduce the risk of the units moving within the load. There are situations when gaps could be required, such as for products that require some cooling or condensation reduction.
- Properly secure the load to the pallet with the correct type of film and wrap pattern.
9. What is the role of a palletizer operator?
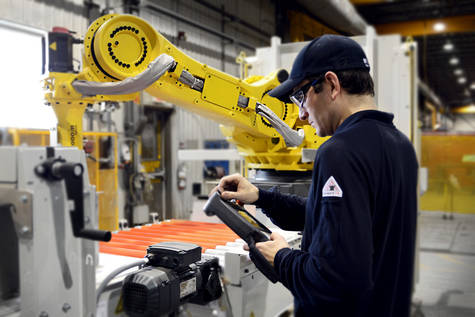
Palletizers, whether conventional or robotic, are designed to not have constant supervision because automation is the ultimate goal and is the case with automatic palletizers. If it is a semi-automatic robot, where pallets are constantly loaded and unloaded, then an employee must be there constantly. Essentially, the higher end the robot, the less supervision is required.
For most operations, the palletizer operator role isn’t necessarily a dedicated one, as the knowledge required isn’t too demanding once the palletizer is built and configured. For instance, a stock person, fork truck driver, or a warehouse supervisor could also be responsible for operating the palletizer. However, when there are multiple machines involved, this increases the need for a dedicated operator.
A palletizer operator selects a pattern configuration that has already been stored on the Human-Machine Interface at a push of a button. They also ensure that there are enough pallets and slip sheets in the magazines for all the loads being created. The operator must perform routine checks to ensure that the equipment is fully operational. Fully loaded pallets are then moved to storage or loaded for transit, typically with a forklift or pallet jack.
If the product on the line changes, then the operator must go into the HMI and reprogram it according to the new product. Lastly, maintenance is a key role in the palletizer operator’s job description, as they may have to replace certain components and clean the equipment when necessary.
Learning to work on these machines can be done by any employee given the proper training. When shopping for palletizers, it is crucial to ask vendors about their training programs. They should have a well-defined series of lessons to bring your employees up to speed on the machine you purchase.
10. How much does a palletizer cost?
A palletizing system’s total cost of ownership depends on operational needs in terms of:
- Required throughput speed
- Level of automation
- End of arm tooling
- Sensors
- Conveyors
- Integration
- Maintenance costs, etc.
Pricing will also vary on whether the system will be manual, conventional, robotic, or hybrid.
Palletizing machines are a long term investment, which includes many factors to consider when making such a purchase. One of these being the upfront cost of the machinery, including shipping, duty, taxes, installation, and employee training. Another is the material and overhead costs, such as electricity, depreciation, and other utilities, which should all be factored into the total cost of ownership. Lastly, upkeep and maintenance costs, along with spare parts, should also be held into account.
For simplicity, we’ll only address the acquisition costs of both conventional and robotic palletizers, as hybrid palletizers are a complex custom solution. The following table breaks down the price of conventional bag and case palletizers, as well as robotic bag and case palletizers, by production rate:
Production Rate | Price Range* (USD) | |
Conventional bag palletizers | Up to 40 BPM | $275,000 - $450,000 |
Conventional case palletizers | Up to 200 CPM | $200,000 - $1,000,000 |
Robotic bag palletizers | Up to 40 BPM | $175,000 - $675,000 |
Robotic case palletizers | Up to 80 CPM | $175,000 - $900,000 |
Boost your packaging operations
Whether you're looking to increase production capacity, replace older units, or improve working conditions, Premier Tech is ready to respond with a state-of-the-art palletizing machine that suits your needs.